Extremely hard materials, exotic shapes: machining tools are often put to the test and their lifespan is sometimes limited. BoostMilling is a roughing strategy that removes material faster while increasing tool life. Let’s find out more about what BoostMilling is and how it can save you money.
Switch from traditional machining to BoostMilling
In traditional machining, the path of a tool on a part to be machined leads to inconsistent material removal, because of the complex geometries. This “pass taking” variable results in overloading the tool. With BoostMilling, machining is “smoother”, for both the tool and the machine.
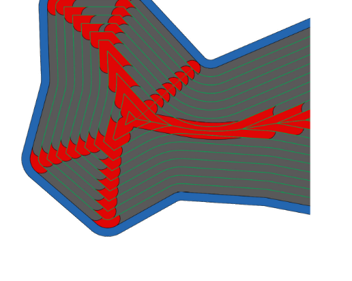
Example of a machining path without BoostMilling: the areas in red are those that are in overload
Step over in traditional machining
Decreasing the step over theoretically reduces the load. Therefore, going from 50 to 10 % of step over reduces the load by 40 %. Nevertheless, even in this configuration, the red areas in the previous diagram remain overloaded.
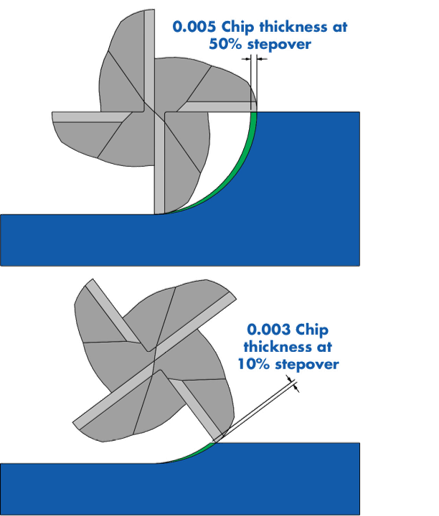
Going from 50 to 10 % of step over reduces the load by 40 %
The problem of the inconsistent angle between tool and material
Traditional tool paths also have two other disadvantages:
- The tool/material angle is too large, greater than 90°;
- This angle varies too much;
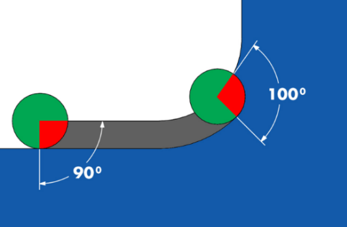
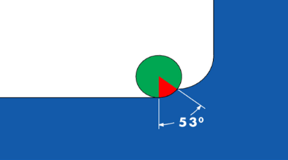
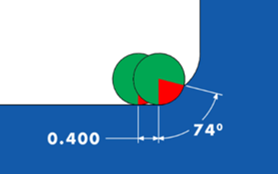
Therefore, if going from 50 to 10% of the step-over reduces the value of this angle, it still remains variable in some areas. The solution is therefore to find a tool path that keeps this angle.
The principle of BoostMilling
BoostMilling allows you to keep a constant pass taking on the entire tool path. How is this possible? By using complex tool paths, you can remove a homogeneous volume of material.
Use the full length of the tool with BoostMilling
In traditional machining, the radial width of each pass is large, greater than 50% of the tool diameter and a shallow depth. The principle of BoostMilling is to reduce this width while increasing the pass depth. This method also has the advantage of using the cutting tool over its entire length, which results in more even wear.
Keep a constant angle with BoostMilling
The power of BoostMilling lies in modifying the tool paths so as to maintain a constant angle. This makes it possible to considerably increase the speed per tooth.
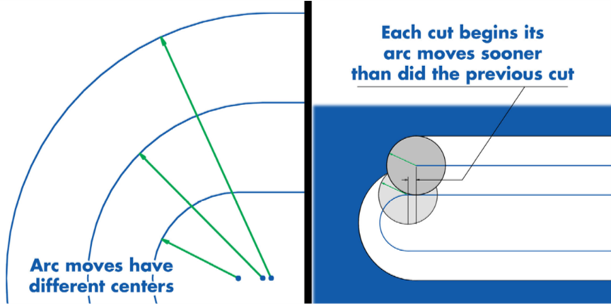
Heat removal and constant pressure
By exerting constant pressure on the tool, not only is the radial pitch reduced, but the pass depth is also increased. The feed rate can be increased to 10 times greater than in traditional machining.
In addition, heat removal is easier with BoostMilling.
TopSolid CAD/CAM Product Range
What are the advantages of BoostMilling?
By choosing to switch to BoostMilling, you will benefit from several advantages that can impact your productivity in the long run.
Reduction of machining time
Although the tool paths are longer in BoostMilling, a high machining depth combined with a high feed rate greatly reduces “chip time”. Therefore, saving 30 to 70% more time is expected with BoostMilling.
For example, 3.5 hours spent in traditional machining operations correspond to 1.5 hours of machining time for a roughing cycle in BoostMilling.
Increased tool life
With BoostMilling, the load is distributed evenly over the entire tool. This means that there is less risk of tool breakage, which increases the lifespan of the tool. In addition, machining operations can be accelerated.
A tool lasts 5 to 10 times longer with BoostMilling.
Machine preservation
Overloading is one of the stresses to which machining machines are regularly subjected, along with vibrations. Overexertion of the tools is usually the cause. By reducing overloads, BoostMilling significantly reduces the stress on the machines.
BoostMilling increases machine life expectancy and reduces maintenance costs
Constant chip volumes
With BoostMilling, the forces on the tool are homogeneous, because the machined volume remains constant. Therefore, the amount of chips produced is also the same throughout the entire machining cycle.
Why is BoostMilling interesting?
The BoostMilling roughing strategy is extremely interesting for machining hard materials, parts with thin walls and during large material removal.
Machining hard materials
BoostMilling is particularly useful for machining hard or exotic materials. Indeed, these materials are difficult to machine and the tool life is greatly reduced with these materials. In addition, tool overloads and the associated heat generation are forcing machinists to reduce machining speeds.
Thin parts
BoostMilling is particularly suitable for machining parts with small wall thicknesses. Indeed, with this soft roughing technique, it is possible to machine as close as possible to the thin walls without the risk of breaking or deforming them.
BoostMilling is an additional TopSolid’Cam module that is aimed at machinists who wish to increase the life of their tools and save machining time. Are you a company concerned with the machining of large titanium parts with complex shapes? In this case, BoostMilling is for you!