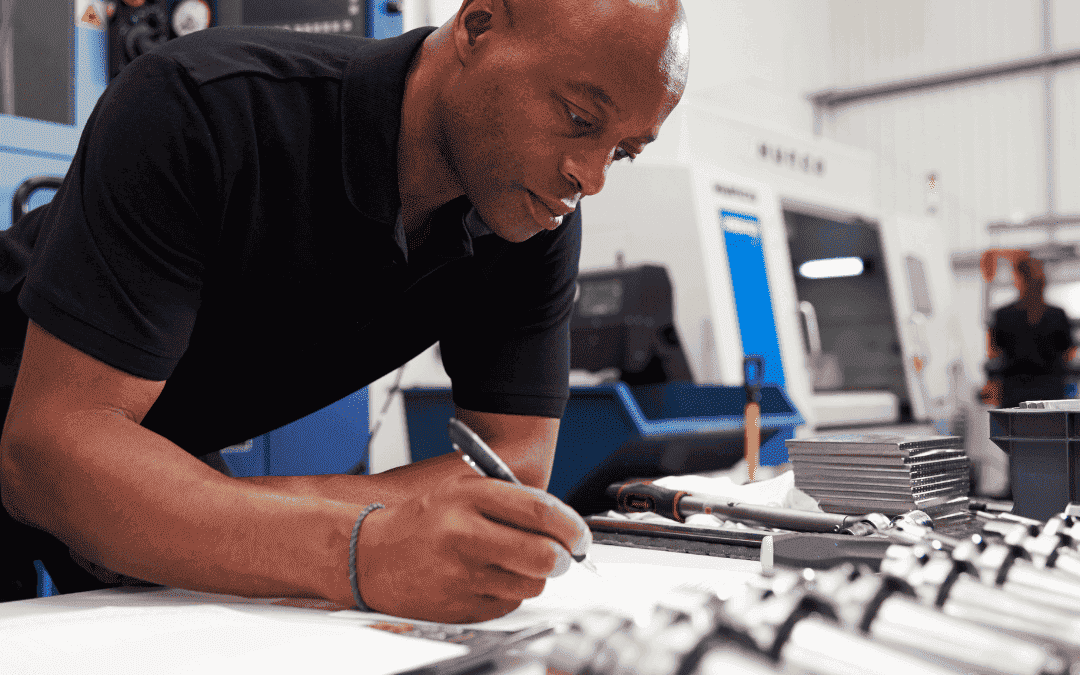
TopSolid’ShopFloor: Reinventing Workshop and Tool Management
Managing tools, programs, and production workflows is a daily challenge for modern workshops—and for good reason. These essential tasks are often time-consuming, error-prone, and fragmented across systems. But what if a fully integrated solution could turn the tide? Discover five key innovations in TopSolid’ShopFloor designed to drive faster, more reliable production.
Workshop Management Today: Key Challenges
Machining workshops face a series of persistent productivity blockers:
- Considerable time wasted searching for tools or programs scattered across multiple machines or systems.
- Frequent errors in assigning programs to the wrong machines, increasing the risk of defects or non-compliance.
- Inadequate tracking of regrinded tools, leading to unnecessary costs and reduced equipment lifespan.
- Fragmented data that undermines communication and coordination among production stakeholders.
5 Innovations Driving Smarter production
TopSolid’ShopFloor is purpose-built to overcome these challenges and elevate the productivity of your workshop or factory. This integrated shop floor management solution is modular, scalable, and adaptable—designed to evolve in real time alongside your operational needs.
1. Streamlined regrinding management
Track and reuse your tooling components effortlessly.
Each component can be easily recorded, tracked and organized for regrinding. Built-in selection and validation features confirm that tools are operational before use— guaranteeing premium machining performance.
2. Sustainable tooling for long-term gains
Regrinding management is part of a sustainable production loop:
- Extended tool lifespan
- Optimized use of resources
- Lower costs and reduced waste
By enabling smarter, more efficient reuse of tooling components, TopSolid’ShopFloor promotes more responsible, cost-effective manufacturing practices.
3. Enhanced productivity through automation
TopSolid’ShopFloor helps you save time without compromising quality, thanks to four key automation features:
- Centralized data on a unified platform
- Real-time access to information for all stakeholders
- Automated workflows that reduce error risk
- Seamless integration with your entire production ecosystem—including ERP systems
The result: clear, consistent access to the right information at the right time—empowering your teams and increasing productivity by 20% to 50% through superior data management.
Consistent tool performance
The introduction of macros for tool parameters marks a major step forward in automation. Previously, only fixed values could be assigned to tool parameters, requiring manual adjustments based on specific needs.
Now, users can define intelligent macros that automatically apply the appropriate parameter values based on each tool’s properties. This eliminates the need for manual intervention, saving valuable time and significantly reducing errors.
5. Unified interface for TopSolid’Cam and ShopFloor Program Manager
The integration between TopSolid’Cam and TopSolid’ShopFloor’s Program Manager has been significantly enhanced. Program numbers are now assigned automatically, and CAM files are directly linked to ISO files.
This seamless connection streamlines workflows, minimizes errors, and ensures full traceability across the manufacturing lifecycle, from design to production.
The range of CAD, CAM, ERP and PDM TopSolid solutions
The Modular Power of TopSolid’ShopFloor
TopSolid’ShopFloor is built around a flexible, modular architecture—ensuring it can adapt to the specific requirements of any workshop.
Project Manager Module
Whether or not TopSolid is installed on the client workstation, Project Manager enables full TopSolid project management directly within TopSolid’ShopFloor. Create and manage customer, project, and contact data. Easily access folders and add documents via simple drag-and-drop.
Program Manager Module
This module can manage all NC program formats and associated manufacturing data, regardless of origin—whether from TopSolid or another CAM solution.
Key advantage: Advanced search tools and a complete history of changes and movements provide powerful support for traceability across your operations.
Tool Manager Module
Integrated for maximum efficiency, Tool Manager allows for proactive management of tool components, assembled tools, and all auxiliary items required in the manufacturing process. It features targeted search capabilities and a wizard to simplify the assembly and disassembly of tools.
Operators also benefit from detailed status reports for better coordination and readiness.
Tool Set Module
This tool configuration history module saves time during setup. It offers advanced features such as 3D visualization, batch tool presetting, and storage of the last preset cycle used for each tool.
Workholding Manager Module
This module simplifies the search and management of tools and components using specific filters or Datamatrix identification input.
Stock Manager Module
Three major functions in one module:
- Full control over your inventory of components and assemblies, including supplier relationships
- Easy creation of purchase orders
- 3D component visualization via integrated TopSolid’Viewer technology
Storage Manager Module
This module provides full 3D visualization of your storage areas, enabling smart and structured management of tool component, assembled tool and workholding device locations. It also includes a permission system for handling tool reservations and user access.
Why Choose TopSolid’ShopFloor?
TopSolid’ShopFloor is far more than workshop management software— it’s a game-changing solution that transforms your entire production chain. By centralizing data, automating repetitive tasks, and streamlining processes, it drives operational excellence at every level:
- Increase productivity by 20% to 50% through better information flow
- Reduce errors and production downtime
- Optimize resource efficiency
- Extend the lifespan of tools and equipment
- Improve communication across teams
- Scale flexibly as your operations evolve
Ready to see TopSolid’ShopFloor in action? Contact us for a free, personalized demo tailored to your workshop’s needs.