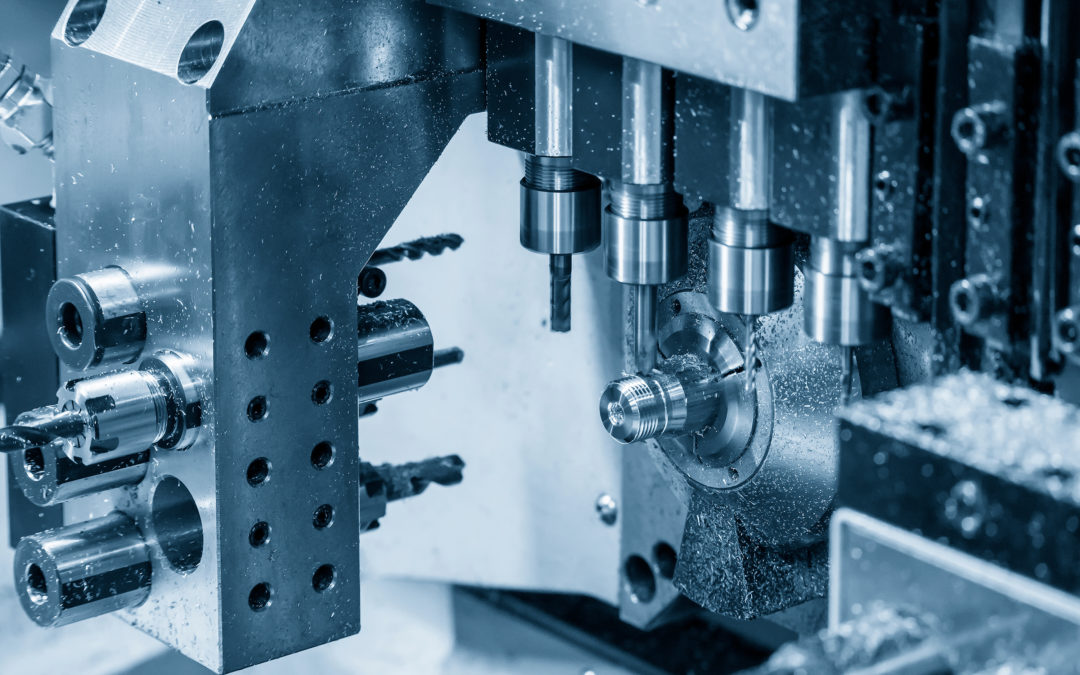
The Swiss Turn Revolution: Advanced Precision, Innovation and Machining Solutions
Swiss Turn, a machining technique that comes from the watchmaking industry, is now a core feature of precision manufacturing. Technological improvements over the years have fine-tuned a method which is now capable of producing the extremely precise mechanical parts used in a variety of sectors, including the automotive industry, electrical appliances and electronics. In this article, we take an in-depth look at this fascinating technique and how it has embraced digitalisation, with a special focus on TopSolid’Cam SwissTurn, a revolutionary feature.
Description and Background
Swiss Turn refers to a technique for machining very small parts with an extremely high degree of precision, up to a thousandth of a millimetre. Originally developed for the watchmaking industry, the technique has evolved and adapted to the precision and productivity requirements of other industries.
Technology and Development
Modern Swiss Turn machines are equipped with numerical controls and capable of performing a whole host of operations including turning, milling and drilling: proof of the technique’s spectacular development over the years. Digitalisation has led to shorter series change times and the ability to produce ever more complex parts.
Challenges and Software Solutions
Given the challenges related to the complexity of the machines involved, and the need to optimise machining times, an appropriate software solution was essential. TopSolid’Cam SwissTurn is a game-changer in that respect, offering precision and flexibility, as well as full integration with the TopSolid platform. The solution makes it easier to manage bar feeders, optimises cycle times and offers multi-channel synchronisation, guaranteeing unbeatable productivity.
Why opt for TopSolid’Cam Swiss Turn?
- Precision and Flexibility: Unlimited management of axes and channels, so it adapts to different machine configurations.
- Integration and Advanced Management: Fully integrated with TopSolid, guaranteeing effective management of rough materials and data.
- Optimised Chip Times: Sophisticated technology for maximum productivity and lower cycle times.
- Multi-Channel Synchronisation: Optimised use of multi-channel machines, avoiding potential conflicts for maximum production output.
See you at SIMODEC!
The SIMODEC trade fair, to be held from 4 to 8 March in La Roche-sur-Foron, provides a great opportunity to discover the outstanding performance of TopSolid’Cam Swiss Turn. Come along to our booth to watch live demonstrations and see for yourself why Swiss Turn is renowned for its precision and performance. The trade fair is a must for everyone looking to optimise their Swiss Turn processes and stay at the forefront of technology.
The Swiss Turn technique is essential for producing high-precision mechanical parts and has been greatly enhanced by technological innovation and the arrival of software solutions such as TopSolid’Cam Swiss Turn. The winning combination of precision, flexibility and optimisation make Swiss Turn a constantly evolving field, and the perfect answer to the challenges of modern industry.