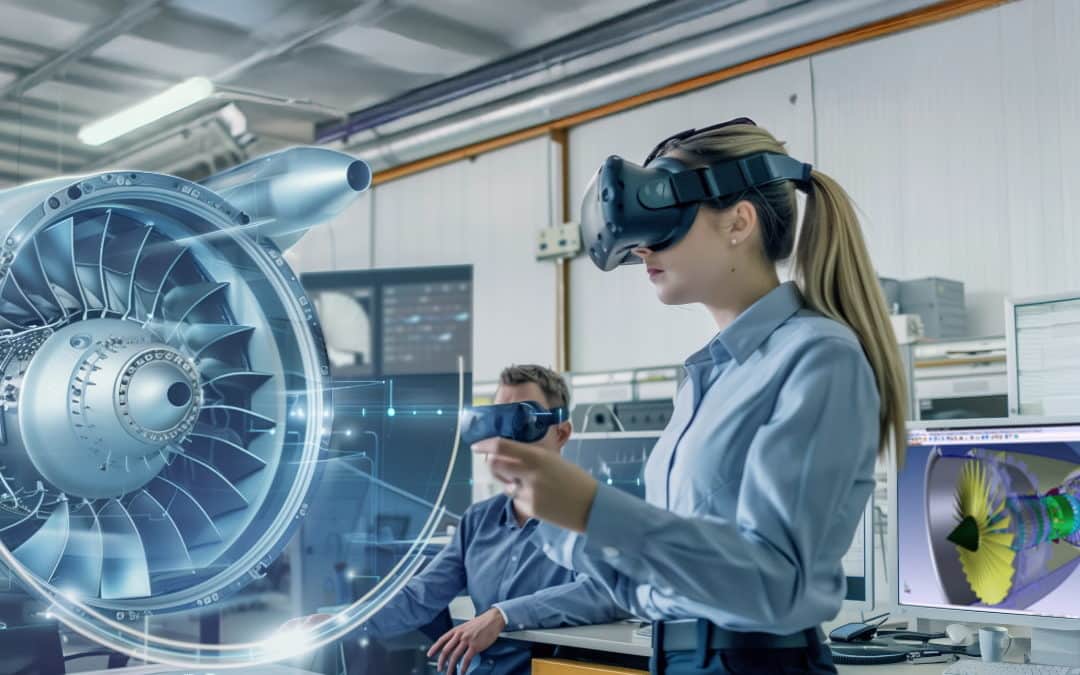
TopSolid’Predict: Unlocking the Power of AI-Enhanced CAD
Renowned for its ability to optimize workflows, artificial intelligence (AI) has secured a strategic place at the heart of industrial processes. Applied to CAD, it dramatically accelerates design while minimizing the risk of error through powerful predictive capabilities. Introducing TopSolid’Predict — TopSolid’s AI solution, engineered to enhance both the efficiency and security of your design projects.
Why Traditional CAD is Reaching its Limits?
The golden era of traditional CAD is coming to a close. While it has long played a pivotal role in transforming design processes, today’s industrial demands for speed and productivity are exposing its limitations.
Searching for previously used commands from past projects slows down operations and forces teams to repeatedly reset their workflows. Add the repetitive, tedious nature of many design steps — a fertile ground for human error — and you risk compromising the integrity of your projects, with costly consequences.
Moreover, traditional CAD solutions are often used in isolation, without intelligent tools to streamline or learn from user habits. This limits systems’ capacity to improve over time — even though they could evolve automated behaviors and design intelligence based on historical data.
In the face of increasing project complexity, these constraints highlight the growing relevance — and necessity — of CAD systems enhanced by AI and automation.
How TopSolid’Predict is Transforming Design?
AI offers a powerful response to the limits of traditional CAD. TopSolid’Predict integrates an innovative predictive engine that analyzes designers’ habits in real time and proactively suggests next actions.
This cutting-edge technology fundamentally redefines design processes, dynamically adapting to the unique working style of each user.
Security is also at the core: TopSolid’Predict operates on a fully local architecture. All data used for learning and predictions is stored internally — guaranteeing absolute confidentiality, with no external data transmission.
These real-time, context-aware recommendations bring immediate value:
- Considerable time savings through automation of repetitive tasks
- A substantial reduction in human error, thanks to precise and relevant suggestions
All of this, with no Internet connection required, and no compromise on data security.
What Benefits Does it Offer Your Design Office?
Integrating predictive AI into your workflows offers a profound transformation of your engineering team’s working experience. By automating repetitive and time-consuming tasks, designers are freed to focus on innovation and creativity — the true engines of added values.
Read also – How collaborative design and digital engineering are revolutionizing the work of design offices?
By leveraging validated historical data, predictive AI also strengthens the reliability of your new designs.
Overall, with context-driven suggestions, TopSolid’Predict fosters a virtuous circle by reducing:
- The risk of human error
- Manual interventions
- Corrective iterations and last-minute revisions
- Non-conformities
TopSolid’Predict places personalization at the heart of your design environment. The interface gradually adapts to each user’s specific working methods, creating a natural synergy between human and machine. The result? A CAD experience that becomes less technical, more intuitive, and consistently delivers high-quality deliverables, whatever the project.
The range of CAD, CAM, ERP and PDM TopSolid solutions
Why Now Is the Time to Embrace AI in CAD?
As projects grow increasingly complex and deadlines tighter, adopting AI-driven CAD is no longer optional — it’s a strategic imperative. Early adopters of this technological shift are positioning themselves as pioneers in a sector undergoing profound transformation, securing a strong competitive edge.
AI is not just another tool: it is reshaping the industry, setting new benchmarks for productivity, efficiency and design excellence.
Ready to experience these benefits for yourself? TopSolid invites you to test TopSolid’Predict. Contact us today and take the first step toward AI-powered CAD — turning today’s challenges into tomorrow’s opportunities for innovation.