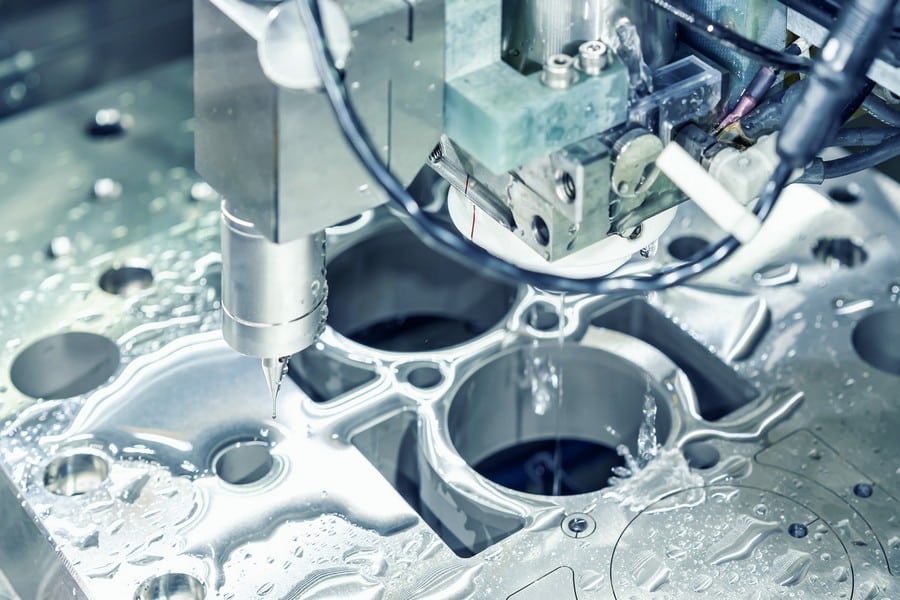
Bearbeitung von Werkstücken: eine vollständige Anleitung!
Bearbeitung von Werkstücken: Definition
Was ist mit der Bearbeitung von Werkstücken eigentlich gemeint?
Die Bearbeitung ist ein Fertigungsprozess, der darin besteht, Rohmaterial, wie z. B. Metall, Kunststoff oder Holz, durch das Entfernen von Masse zu formen, um ein fertiges Bauteil mit genauen Abmessungen und spezifischen Merkmalen zu erhalten. Ob Automobilindustrie, Luft- und Raumfahrt, Energiesektor, Elektronik usw. … die Bearbeitung von Werkstücken ist eine Methode, die in der Industrie weit verbreitet ist.
Hauptziel der Bearbeitung ist es, mit hoher Genauigkeit komplexe Formen und fertige Oberflächen herzustellen. Dazu gehört je nach den technischen Spezifikationen des Endprodukts die Schaffung von Hohlräumen, Nuten, Gewinden, Bohrungen sowie ebenen oder geschwungenen Flächen.
Zu den Hauptvorteilen der Bearbeitung zählt ihre Vielseitigkeit. Sie kann zur Fertigung einer großen Auswahl unterschiedlichster Bauteile eingesetzt werden, von einfachen Einzelteilen bis hin zu komplexen Baugruppen. Darüber hinaus eignet sich die Bearbeitung für unterschiedliche Arten von Material, insbesondere eisenhaltige und nicht eisenhaltige Metalle, technische Kunststoffe oder Verbundwerkstoffe.
Zoom auf Bearbeitungsmaschinen
Der Bearbeitungsprozess erfordert die Verwendung einer Werkzeugmaschine, wie z. B. Dreh- oder Fräsmaschinen bzw. Schleif- oder Bohrmaschinen, die präzise gesteuert werden, um Material schrittweise und methodisch zu entfernen. Je nach den spezifischen Anforderungen des Bearbeitungsvorgangs werden verschiedene Schneidwerkzeuge, wie z. B. Bohrer, Fräsen, Reibahlen und Klingen verwendet.
Durch die Einführung neuer Technologien und Techniken hat sich die Bearbeitung im Laufe der Jahre weiterentwickelt. Moderne Werkzeugmaschinen werden in zunehmendem Maße automatisiert und integrieren CNC-Systeme sowie hochentwickelte Sensoren, um die Präzision, die Produktivität und die Sicherheit der Bearbeitungsvorgänge zu verbessern. Heutzutage verwenden die meisten Unternehmen CNC-Maschinen mit einem Computersystem (CAM), um den Bearbeitungsprozess teilweise oder vollständig zu automatisieren.
Welche Aufgaben erfüllt ein Bearbeitungstechniker?
Ein Bearbeitungstechniker ist eine Fachkraft, die auf die Durchführung von Bearbeitungsvorgängen spezialisiert ist. Sie trägt die Verantwortung für die Vorbereitung und Einrichtung der Werkzeugmaschinen, die Wahl der geeigneten Schneidmaschinen, die Einstellung der Schneidparameter und die Durchführung der Bearbeitungsvorgänge. Dazu muss diese Fachkraft technische Zeichnungen lesen und interpretieren können, je nach den Spezifikationen die richtigen Bearbeitungsmethoden auswählen und die Maschinen und Messinstrumente korrekt verwenden, um die Konformität mit den erforderlichen Toleranzen zu gewährleisten.
Neben diesen technischen Fähigkeiten muss der Bearbeitungstechniker über ein umfassendes Fachwissen bezüglich Materialien, Bearbeitungsprozesse und Sicherheitsnormen verfügen. Außerdem muss er in der Lage sein, potenzielle Probleme zu analysieren, Fertigungsmängel zu beseitigen und korrektive Maßnahmen zu ergreifen, um die Qualität der Werkstücke zu gewährleisten. Aufgrund der rasanten Entwicklung in der Bearbeitungsindustrie müssen sich Bearbeitungstechniker regelmäßig über neue Technologien und Fortschritte informieren. Sie können durchaus aufgefordert werden, an hoch modernen Werkzeugmaschinen zu arbeiten, CNC-Systeme zu integrieren und CAD-Softwares für die Optimierung des Bearbeitungsprozesses zu verwenden.
Was sind die 4 Grundbearbeitungsvorgänge?
Drehen
Mit einer Drehmaschinen können zylindrische bzw. konische Teile oder auch Teile mit komplexen Formen, wie z. B. Gewinde oder Nuten, hergestellt werden. Dazu wird das Werkstück auf einer Drehspindel fixiert, während sich das Schneidwerkzeug am Werkstück entlang bewegt, um Material zu entfernen und dem Teil die gewünschte Form zu geben.
Fräsen
Mit einer rotierenden Fräsmaschine wird Material entfernt, um komplexe Formen, wie z. B. Nuten, ebene Flächen, Löcher oder Konturen zu schaffen. Fräsmaschinen können je nach den Bewegungen des Bauteils und des Schneidwerkzeugs für die 2D- oder 3D-Bearbeitung eingesetzt werden.
Für das Fräsen präziser ebener Flächen mit einer glatten Oberfläche wird eine besondere Fräsmaschine verwendet. Ebene Flächen dienen oftmals dem Zweck, eine Auflagefläche oder Referenzflächen an Teilen zu schaffen.
Bohren / Ausdrehen / Gewindeschneiden
Beim Bohren werden mithilfe eines Bohreinsatzes Löcher in ein Bauteil gebohrt. Der Bohreinsatz dreht sich und dringt in das Teil ein, indem er Material entfernt und ein Loch mit einem genauen Durchmesser und einer genauen Tiefe bohrt. Die Bohrung kann mit einer herkömmlichen Bohrmaschine oder mit einer modernen Werkzeugmaschine durchgeführt werden.
Ergänzend dazu wird durch das Gewindeschneiden ein Gewinde in ein zuvor gebohrtes Loch geschnitten. Mit einem Gewindeschneider lassen sich Nuten in Form eines Gewindes in ein Loch schneiden, um anschließend Bolzen und andere Gewindeelemente einschrauben zu können.
Durch das Ausdrehen kann ein Loch, das zuvor in ein Bauteil gebohrt wurde, vergrößert und seine Qualität verbessert werden. Dieser Vorgang wird in der Regel durchgeführt, wenn genaue Toleranzen, hochwertige Oberflächenausführungen oder spezifische Abmessungen erforderlich sind.
Schleifen
Das Schleifen ist ein hochpräziser Bearbeitungsvorgang mit dem Ziel, besonders glatte Flächen mit genauen Abmessungen zu erhalten. Dieser Vorgang wird mithilfe einer Schleifmaschine durchgeführt, die mit Schleifscheiben ausgestattet ist, um kleine Mengen Material zu entfernen und hochgenaue Toleranzen zu erhalten.
Diese Bearbeitungsvorgänge bilden die Grundlage für zahlreiche hochmoderne Bearbeitungstechniken. Je nach den Spezifikationen der zu bearbeitenden Werkstücke, den erforderlichen Toleranzen und erwünschten geometrischen Merkmalen ist es wichtig, den richtigen Bearbeitungsvorgang zu wählen.
Die Palette der CAD, CAM, Lösungen TopSolid
Wie sieht die Zukunft der Bearbeitung aus?
Im Bereich der Bearbeitung sehen wir mehrere allgemeine Trends.
Zunehmende Automatisierung
Mit der Einführung von Robotern und intelligenten Fertigungssystemen beobachten wir eine zunehmende Automatisierung in der Bearbeitung. Moderne Werkzeugmaschinen sind mit hochmodernen Sensoren, CNC-Steuerungen und KI-Technologien ausgestattet, um im Produktionsverfahren die Präzision und die Geschwindigkeit zu optimieren und menschliche Fehler zu verringern.
3D-Druck für die Bearbeitung
Bei der Bearbeitung kommt immer häufiger der 3D-Druck zum Einsatz, insbesondere bei der Fertigung komplexer Teile. 3D-Druck-Technologien für Metall ermöglichen tatsächlich die Fertigung von Teilen mit komplexen internen Geometrien, was die Notwendigkeit zusätzlicher Bearbeitungsvorgänge verringert. Die Integration des 3D-Drucks in die traditionellen Bearbeitungsmethoden eröffnet außerordentlich flexible Design- und Fertigungsmöglichkeiten.
Hybride additive Fertigung
Die hybride additive Fertigung kombiniert den 3D-Druck mit der herkömmlichen Bearbeitung. Dieser Ansatz ermöglicht die Konstruktion von Teilen mit komplexen Strukturen unter Verwendung des 3D-Drucks und die anschließende Bearbeitung, um fertige Oberflächen, genaue Toleranzen oder zusätzliche Funktionen zu erhalten.
Integration künstlicher Intelligenz
Die Verwendung der künstlichen Intelligenz (KI) in der Bearbeitung expandiert. KI kann verwendet werden, um Daten von Werkzeugmaschinen in Echtzeit zu analysieren, Schneidparameter zu optimieren, Fertigungsmängel zu erkennen und die Effizienz des Bearbeitungsprozesses insgesamt zu verbessern.
Nachhaltigkeit und Umweltverantwortung
Die Bearbeitung wird in Zukunft sehr viel stärker auf die Nachhaltigkeit und die Umweltverantwortung ausgerichtet sein. Unternehmen werden sich bemühen, ihren ökologischen Fußabdruck zu reduzieren und zu diesem Zweck energiesparende Bearbeitungsverfahren einführen, recyclingfähige Material verwenden und Prozesse optimieren, um Abfälle zu verringern.
Ob Medizintechnik, Luft- und Raumfahrt, allgemeiner oder präziser Maschinenbau, Gießerei oder Folgeverbundwerkzeuge, Uhrenindustrie, Brillenherstellung oder maschinengeschweißte Teile, TopSolid’Cam bietet jeder Branche die am besten geeignete Bearbeitungslösung! Unsere verschiedenen Module bieten eine Vielzahl technischer Lösungen für Ihre Anforderungen beim 2D- oder 3D-Fräsen mit 4 oder 5 Achsen in fester oder stufenloser Position wie auch beim Drehen oder Automatendrehen. Sie möchten mehr erfahren? Kontaktieren Sie uns!