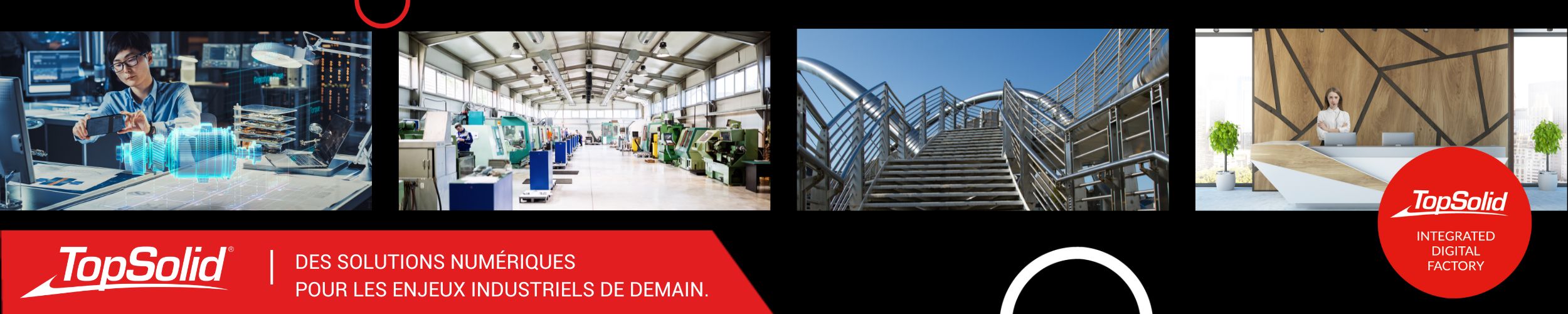
TopSolid’Predict : la puissance de l’IA intégrée à la CAO
TopSolid’Predict révolutionne la CAO en intégrant l’intelligence artificielle et la réalité augmentée. Découvrez comment ces technologies transforment la conception numérique et optimisent les processus industriels
Logiciel GPAO : optimisez la gestion de votre production
Découvrez comment préparer, sélectionner et implémenter la solution idéale de GPAO, de la définition des objectifs à l’accompagnement post-installation. Grâce à des conseils concrets, vous améliorez la coordination, la traçabilité et la réactivité de votre atelier. Un guide clair pour réussir votre transition vers l’industrie 4.0.
Modélisation 3D : tout ce qu’il faut savoir !
La modélisation 3D est devenue incontournable dans de nombreux secteurs. Cet article vous explique comment elle fonctionne, à quoi elle sert et avec quels outils la pratiquer. De la conception à la simulation, découvrez tout ce que la 3D apporte à vos projets.
Transformer l’artisanat et le fraisage du bois grâce aux logiciels CAO
Le fraisage du bois évolue, entre précision artisanale et puissance numérique. Cet article explore comment les logiciels de CAO permettent de moderniser l’atelier sans renier les savoir-faire. Conception 3D, optimisation des découpes, gain de temps… la technologie devient un véritable allié !
TopSolid’Wood : la solution complète et intégrée pour l’industrie du bois
TopSolid’Wood est une solution logicielle tout-en-un dédiée à l’industrie du bois. Elle offre aux artisans, agenceurs et fabricants une chaîne de production optimisée, de la conception 3D à la fabrication, avec des outils puissants pour gagner en précision, en productivité et en qualité. Découvrez comment, en détail, dans cet article !
Réalité virtuelle industrielle ou comment transformer sa chaîne de production
Intégrer la réalité augmentée dans les opérations industrielles c’est bénéficier d’une multitude d’avantages comme entre autres : améliorer la productivité, réduire les erreurs et optimiser la formation. Découvrez comment TOPSOLID transforme votre chaîne de production.
Maintenance prédictive : révolutionner la gestion des actifs industriels
Pour une gestion des actifs industriels efficace et optimisée, la maintenance prédictive fait appel à des technologies avancées dans le but d’anticiper les défaillances des équipements et de prolonger leur durée de vie. Entrez dans l’ère de l’industrie 4.0 grâce à TOPSOLID.
Formation CAO : la clé pour maîtriser la conception 3D et le modélisme
La CAO s’est imposée comme un élément incontournable dans la conception 3D et du modélisme. Les formations TOPSOLID vous permettent de rester à la pointe de la technologie et d’exploiter pleinement les nouvelles fonctionnalités des logiciels.
Le PDM : qu’est-ce que c’est ?
Aujourd’hui, le PDM (Product Data Management) fait figure d’outil indissociable de la performance industrielle. En effet, à l’heure de l’usine 4.0, les enjeux liés à la compétitivité et la productivité imposent la capacité à accéder à une information précise, à jour, et à chaque moment du cycle de vie du produit.
Logiciel GED : tout ce qu’il faut savoir
Centraliser les documents, fluidifier les échanges d’informations, fiabiliser les processus : une solution GED bien intégrée transforme la gestion documentaire en véritable levier de performance industrielle. De l’indexation automatique à la conformité réglementaire, chaque fonctionnalité joue un rôle clé dans l’efficacité au quotidien.
ERP industrie : quel rôle dans l’industrie 4.0 ?
Face aux exigences croissantes de réactivité, de personnalisation et d’optimisation des ressources, l’ERP s’impose comme un levier essentiel pour les industriels. Découvrez comment cet outil centralise les flux d’information, pilote l’activité en temps réel et soutient la transformation digitale des entreprises vers l’usine du futur.
TopSolid’Automation : l’automatisation à portée de main
Découvrez TopSolid’Automation, l’API officielle de TopSolid, conçue pour automatiser vos processus CAD/CAM et booster votre productivité. Intégrez vos outils, créez vos scripts, explorez le Developer Center et rejoignez la communauté !
Et si votre CAO était obsolète ? Lumière sur les alternatives dans l’air du temps
Les solutions de CAO traditionnelles montrent leurs limites face aux nouvelles attentes des bureaux d’études. Découvrez pourquoi TopSolid, avec son approche évolutive et intégrée, offre une alternative moderne et efficace pour répondre aux défis de la conception assistée par ordinateur
TopSolid’ShopFloor transforme la gestion de votre atelier et de vos outils
On le sait : la gestion des outils, des programmes et des flux de production représente un défi quotidien pour votre atelier. Et pour cause, ces tâches sont souvent source de perte de temps et d’erreurs. Et si l’implémentation d’une solution intégrée pouvait changer la donne ? Lumière sur 5 nouveautés de TopSolid’ShopFloor au service d’une production efficace.
Boostez votre performance industrielle avec TopSolid’Monitor
Le suivi en temps réel des machines est essentiel pour éviter les pertes de performance et de rentabilité. TopSolid’Monitor offre une solution efficace avec des tableaux de bord, des analyses automatisées et un déploiement rapide, permettant aux usines d’optimiser leur productivité et de réduire les arrêts non planifiés.
Programmation CNC : comment maximiser productivité et précision ?
La programmation CNC (Computer numerical control) est devenue un élément clé de l’industrie manufacturière moderne, offrant une précision inégalée et une productivité accrue. Cet article vise à répondre à plusieurs questions cruciales sur la programmation CNC, en expliquant ses principes de base, ses applications, et les meilleurs logiciels disponibles.
Migration ERP : surmonter les défis pour transformer votre entreprise
Utilisés pour centraliser un certain nombre de tâches de gestion, les logiciels ERP (Enterprise Resource Planning) couvrent plusieurs fonctions au sein des entreprises : gestion des finances, ressources humaines, production, achats et ventes… Ce type de solution favorise l’efficacité opérationnelle grâce à l’accessibilité des données en temps réel d’un service à l’autre – non sans cadre pour des questions de sécurité et de confidentialité.
L’usinage CNC, une pratique qui révolutionne la fabrication de précision
L’usinage CNC (Computer numerical control) ou, en français, l’usinage par Machines-Outils à Commande Numérique (MOCN) est un processus de fabrication soustractif. Concrètement, il consiste à façonner des pièces par suppression de matière, via des commandes numériques. Ces MOCN, intégrant des fraiseuses, des tours et des découpeuses, sont programmées pour exécuter des opérations précises avec un niveau de répétabilité élevé.
Fabrication additive métallique et usinage : fusionner les technologies pour l’innovation
Incontournable en industrie – et notamment en métallurgie –, la fabrication additive permet de multiplier les possibilités en matière de production. Une innovation indispensable pour votre compétitivité et votre attractivité, le but étant d’être en mesure de proposer à vos clients et prospects l’utilisation de nouvelles technologies. Découverte.
Suivi de production industrielle : au cœur de l’automatisation des process
Le suivi de production industrielle a toujours reposé sur la collecte et l’analyse d’un certain nombre de données, à différents moments du processus. Face à des enjeux financiers et de productivité toujours plus forts, comment faire pour optimiser cette opération ?