Le contrôle de pièces mécanique permet d’une part de vérifier le respect des spécifications du produit au cours de la production, et d’autre part, de prouver au client final la bonne conformité de ce qui a été fabriqué. Service qualité, service méthodes, opérateurs machines, magasiniers… Processus transverse dans l’entreprise, le contrôle de pièces fait intervenir de nombreux acteurs pour générer un livrable client, si bien qu’il est primordial d’assurer une bonne circulation de l’information, dans une optique d’Usine 4.0. A ce titre et bien d’autres, il est avantageux de dématérialiser le processus de contrôle de pièces.
Les limites d’un contrôle de pièces « à la main »
Selon le domaine d’activité, la complexité de la pièce ou les exigences du client, les contrôles s’opèrent à la première pièce (FAI -First Article Inspection), à chaque pièce par un opérateur au pied de la machine (auto-contrôle), voire à un contrôle final avant livraison.
La première étape du processus de contrôle qualité est le relevé de cotes. Cette étape vise à récupérer les caractéristiques à contrôler à partir du support de départ, qui peut ne pas être le même selon le type de contrôle. La construction du plan de contrôle FAI s’effectue sur le plan 2D fourni par le client (généralement au format PDF), alors que le plan d’auto-contrôle peut être construit à partir des plans 3D de chaque phase de fabrication conçus à partir d’une CAO.
Cette étape peut être réalisée par le service Qualité et parfois par le bureau des méthodes, via une saisie manuelle généralement dans un fichier Excel ou dans l’ERP. Les documents attendus à cette étape sont le plan bullé portant l’identification des cotes à contrôler et le plan de contrôle (la liste des caractéristiques à contrôler et leurs tolérances).
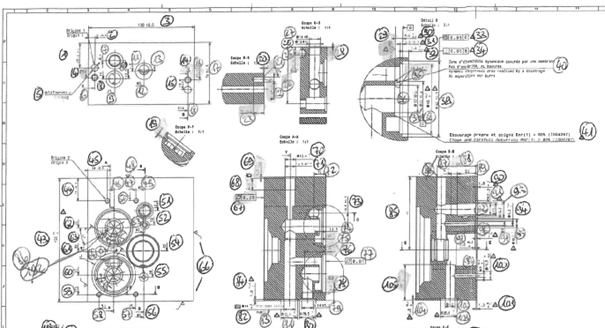
Une fois la liste des caractéristiques à contrôler effectuée, la deuxième étape est l’acquisition des mesures soit par le personnel contrôleur, soit par des logiciels tiers de mesure tridimensionnelle. Cette étape nécessite des données propres à l’ordre de fabrication pour connaître notamment le nombre de pièces à produire dans la série. Généralement c’est un format papier ou Excel qui est utilisé. Cette étape peut être réalisée par le service Qualité (FAI, contrôle final), par les opérateurs au pied de la machine (auto-contrôle) ou par le magasinier (contrôle à réception fournisseur / sous-traitance).
Enfin, il incombe en dernier lieu au service Qualité d’interpréter les résultats de mesure à l’aide de modèles probabilistes et d’indicateurs de statistique des procédés. Cette dernière étape sert à définir les stratégies de contrôle et à affiner les fréquences de contrôle des différentes typologies de cotes.
Perte de temps et risques d’erreurs
Lecture du plan, dessin de la bulle à main levée ou via un éditeur de PDF, saisie de la valeur de cote à contrôler sur le support (Excel, papier, ERP), recherche des tolérances dans le tableau de norme, saisie des tolérances dans le support… Lorsqu’il est effectué manuellement, le bullage du plan est très chronophage. Et si une nouvelle version du plan de pièce avec des modifications arrive, le travail est souvent à reprendre de zéro.
Par ailleurs, avec un processus de saisie manuelle, les risques d’erreur de saisie et d’erreur de lecture dans le tableau de normes ne sont pas négligeables.
Travailler avec un support papier ou un fichier Excel pose également un problème de stockage et de traçabilité. Sans compter que le support papier n’est pas idéal dans un atelier de production, du fait des risques de détérioration, traces ou ratures. Ainsi, lorsque la preuve de contrôle doit être envoyée au client, il est fréquent de devoir re-saisir des informations pour mettre au propre.
Enfin, les données n’étant pas informatisées, il n’est pas possible d’établir des indicateurs décisionnels ou de retracer les ressources utilisées.
Pour toutes ces raisons, il est vivement recommandé d’informatiser le processus de contrôle de pièces.
La gamme de solutions CAO, FAO, PDM et ERP TopSolid
Informatiser son processus de contrôle de pièces : quels avantages ?
Dématérialiser votre processus de contrôle de pièces va vous permettre de gagner en qualité, en fiabilité et en productivité. L’informatisation vous permettra en outre de mieux assurer le partage des données et de favoriser leur réutilisation au sein de l’entreprise afin de gagner en traçabilité, tout en bénéficiant d’une ergonomie adaptée à chaque étape du processus. En somme, voici les principaux avantages d’une telle démarche :
- Gagner du temps
- Lors du bullage
- Lors de la réutilisation du projet
- Limiter les erreurs
- Normes de tolérances et ajustements intégrés au logiciel.
- Capitaliser sur les données
- Stocker et centraliser les mesures de diverses provenances (auto-contrôle, MMT)
- Tracer les contrôles
- Les mesures et les contrôleurs
- Les moyens de contrôle
- Présenter les informations dans un format adapté à chaque étape
- Fournir des éditions propres
TopSolid’Inspection, l’allié de votre contrôle de pièces
TopSolid’Inspection propose une suite de 3 programmes qui couvrent les différentes fonctionnalités attendues dans le processus de contrôle de pièces :
- Le relevé de cotes
- Le relevé de mesure
- L’analyse et statistique des procédés
Voyons dans le détail de quoi il en retourne.
Relevé de cotes
La création d’un Projet d’inspection commence par la saisie d’informations « administratives » (client, référence de pièce, indice, …) et la sélection d’un plan de pièces au format PDF, image (JPG, BMP, TIF) ou vectoriel 2D (DXF/DWG).
Plusieurs cas d’usage peuvent alors être envisagés :
- L’entreprise souhaitant un processus indépendant peut utiliser TopSolid’Inspection en mode stand-alone en créant manuellement chaque projet.
- L’entreprise souhaitant rattacher le processus à son ERP peut développer une passerelle pour une création automatique du projet.
- L’entreprise possédant TopSolid’Erp bénéficie d’une liaison plus intime en standard : création et liaison documentaire du projet en 2 clics, pilotage des relevés de mesure pour chaque ordre de fabrication.
- L’entreprise possédant TopSolid’Design (CAO) peut créer un projet avec récupération automatique des données d’un tableau de cotation d’une mise en plan.
Dans tous les cas, le bullage du plan récupère les caractéristiques par lecture directe des valeurs dans le PDF ou reconnaissance OCR sur les images.
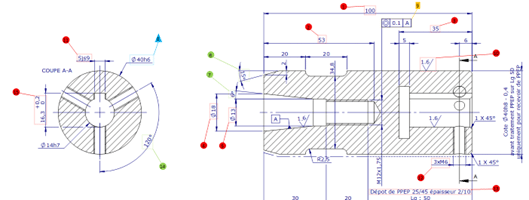
La liste des caractéristiques est complétée avec les informations qualité : tolérances, fréquences de contrôle, moyens de contrôle, phases, traitements de surface…
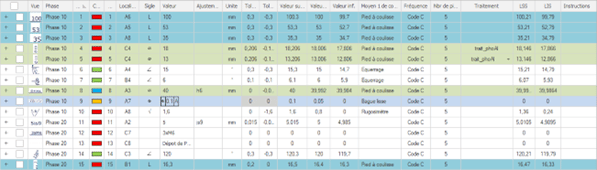
Les sorties sont l’impression du plan bullé, le rapport de contrôle avec mise en page personnalisée, ainsi qu’une extraction des données vers un format d’échange (TXT, Excel, CSV,…) à destination de logiciels tiers.
Au cas où une entreprise ne souhaite pas, dans un premier temps, dématérialiser le relevé de mesure, elle peut éditer les documents qui reprennent le processus « papier » ou « fichier » existant. Ainsi, même si l’entreprise n’est pas mûre pour une informatisation complète, elle y trouve son compte dans le gain de temps et la fiabilité des informations qualité.
D’ailleurs, les entreprises qui se sont prêtées au jeu de la comparaison « ancienne méthode vs méthode TopSolid’Inspection » ont divisé par un facteur de 3 à 4 le temps passé à relever les cotes du plan !
Relevé de mesure
Les informations de l’ordre de fabrication viennent mettre à jour le projet d’inspection. Pour chaque caractéristique, le nombre de pièces à contrôler est recalculé automatiquement en fonction des fréquences de contrôle. Le projet d’inspection peut être ouvert dans l’interface Controller sur les ordinateurs ou tablettes Windows de l’atelier pour une saisie des mesures dématérialisées. Le programme Creator peut aussi être utilisé pour relever des mesures.
Bon à savoir : les mesures peuvent également être récupérées et remontées dans le projet d’inspection depuis un compte-rendu de logiciel tiers (logiciel de tridimensionnelle par exemple).
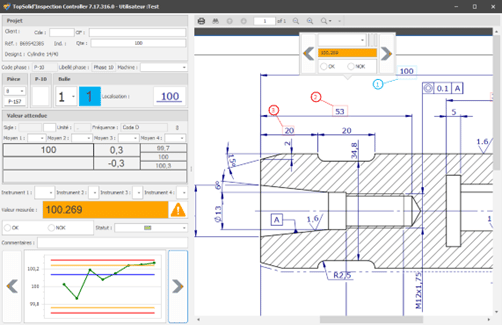
Concrètement : le projet d’inspection est mis à disposition des opérateurs machine de l’atelier sur un ordinateur ou tablette. L’opérateur choisit le poste de travail qui le concerne puis est guidé dans ses contrôles. L’ergonomie de la présentation des données est différente selon le type de contrôle. Des indicateurs visuels (limites de surveillance, carte de contrôle) avertissent d’une dérive des résultats pour suggérer une action corrective. Le rapport de contrôle contenant les résultats est enregistré au format PDF et directement envoyé au client par email.
Analyse et statistique des procédés
Il s’agit du programme d’analyse des résultats qui calcule des indicateurs de statistique des procédés et permet les recherches multicritères dans l’ensemble des projets d’inspection.
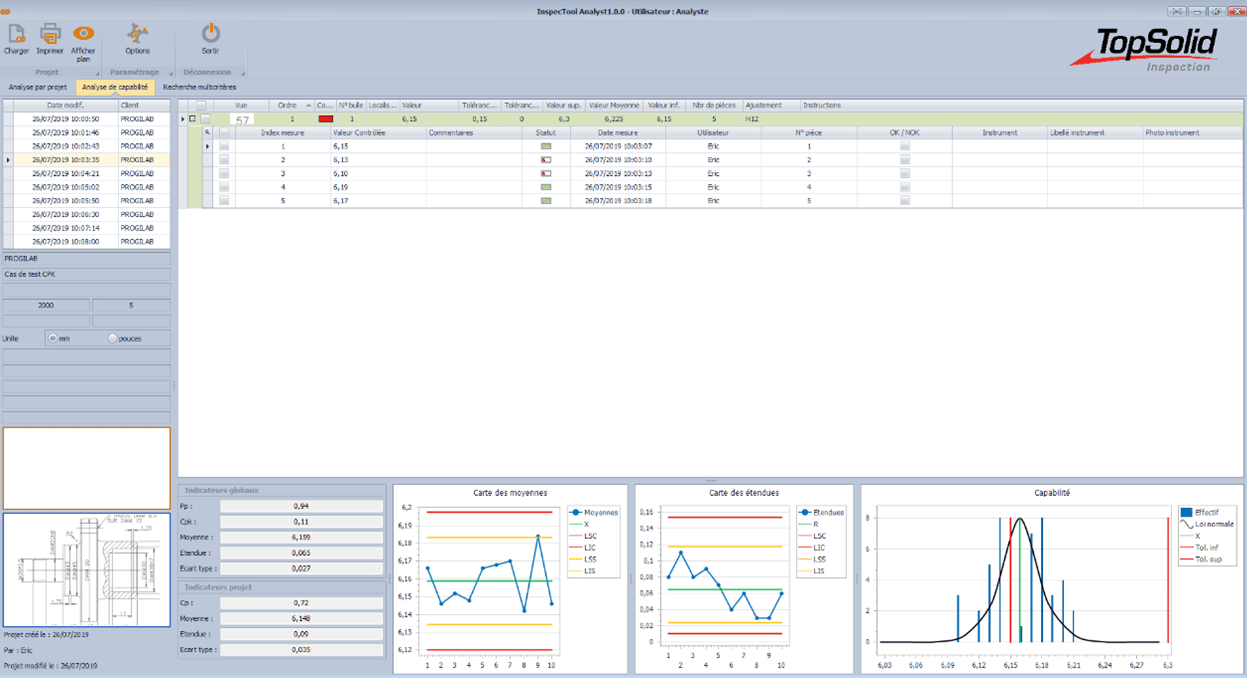
L’analyse des courbes et indicateurs sur plusieurs séries de mesure permet de valider le respect de la tolérance d’une cote dans le temps. La machine est capable de tenir le résultat attendu, le service qualité décide de réduire la fréquence de contrôle de cette cote et ainsi diminuer le temps passé au contrôle.
Si lors d’un audit qualité, l’auditeur demande à trouver les pièces potentiellement impactées par un instrument de mesure détecté comme défectueux, la recherche multicritère permet de répondre à la question et de lister les ordres de fabrication impactés sur une période de temps donnée.
Vous souhaitez en savoir plus sur TopSolid’Inspection ? Contactez-nous !