A ce titre, il est légitime de vouloir s’équiper des meilleurs systèmes de gestion de la production … encore faut-il que tout ce beau monde soit capable de communiquer ! Il en va en effet de la continuité numérique, condition sine qua non à l’optimisation de l’efficacité et de la qualité dans l’industrie. Pour y parvenir, misez sur une solution 360°, TOPSOLID SAS se charge d’accompagner votre démarche.
L’importance d’un processus de transition numérique pour les entreprises de l’industrie mécanique
Le secteur de l’industrie mécanique n’échappe pas aux effets de la mondialisation : concurrence sans frontières, exigences clients extrêmes en termes de délais de mise sur le marché et de diminution des coûts, forte tendance à l’uberisation des offres, le tout agrémenté d’exploitation de la DATA, nouveau Saint Graal stratégique!
L’enjeu consistant à savoir s’adapter vite et bien à la demande, en faisant preuve à la fois de flexibilité, de réactivité et de compétitivité, la transition numérique constitue LA solution … le bouleversement du modèle existant étant compris dans le package !
Rater ce virage, c’est remettre en question, voire tuer la compétitivité de l’entreprise : n’oublions pas que les zones géographiques du globe sont différentes en termes de coûts et qu’une entreprise ayant déjà entamé son évolution vers l’industrie 4.0 sera toujours plus attractive qu’une entreprise au modèle vieillissant. D’ailleurs le numérique représentant aussi un facteur essentiel d’attractivité pour la génération entrant sur le marché, les différents métiers doivent offrir aujourd’hui plus que jamais leur lot de nouvelles technologies. Enfin, les innovations étant corrélées aux avancées technologiques … autant dire qu’une entreprise n’étant pas entrée dans sa transition numérique n’a que peu, voire pas de chances, d’être créative et produire une quelconque nouveauté utile au marché.
En résumé, sans transition numérique, c’est la condamnation de l’entreprise à court terme …
Les gains réalisés par la digitalisation de l’usine des entreprises de l’industrie mécanique
… et par opposition, muter vers l’usine du futur ouvre les portes du produire plus vite et mieux !
Alors oui, le bouleversement du modèle de production pour les entreprises de l’industrie mécanique est réel, mais il n’en reste pas moins LE vecteur de valeur ajoutée. Pourquoi ?
Parce que tout d’abord, il faut savoir que le concept d’usine numérique implique l’interconnexion de tous les systèmes intervenant dans la chaîne de production, et ce, en temps réel. On parle ici de l’ERP, du PDM/PLM, des logiciels de CFAO et des machines-outils… La liste n’étant pas exhaustive, mais cette condition constitue la clé de voûte de l’industrie 4.0.
Dans ce contexte d’ultra communication, l’information est centralisée, unique et toujours à jour pour l’ensemble des services de l’entreprise, du Bureau d’Etudes ou des Méthodes, à l’atelier, en passant par les services administratifs et même les plateformes clients et fournisseurs selon les cas. De fait les saisies multiples, les recherches intempestives des dernières mises à jour et les allers retours chronophages entre les différents départements deviennent de l’histoire ancienne et révolue. On imagine alors aisément le gain de temps en conception.
La fabrication n’est cependant pas en reste. Le modèle numérique d’un produit permet en effet autant de simulations 3D, de tests et de validations avant même la fabrication d’une première pièce, et ce, quel que soit le procédé utilisé. Ces possibilités d’expérimentation virtuelle constituent non seulement un gain de temps précieux, mais également une économie de matière première et d’énergie indéniables.
Constituant majeur de l’usine 4.0, la DATA, combinée aux calculs algorithmiques, permet de mesurer précisément l’efficacité des systèmes de production et de les améliorer en menant des actions en temps réel sur des facteurs d’efficacité ou de qualité des processus métier.
Gain en temps, en coût, en efficacité et en qualité … un modèle basé sur une chaîne numérique répond à 100 % des enjeux vitaux de l’industrie mécanique. Maintenant, qu’en est-il de sa mise en œuvre concrète ?
La gamme de solutions CAO, FAO, PDM et ERP TopSolid
TopSolid Integrated Digital Factory : logiciel de CFAO et de gestion communiquant au service de l’industrie mécanique
Réussir son passage à l’usine numérique passe d’abord par deux essentiels :
- l’anticipation des besoins de l’entreprise
- la traduction des besoins en termes d’interopérabilité des systèmes de gestion mis en place.
L’exercice est périlleux, nous vous l’accordons, une petite omission pouvant entraîner une perte de temps colossale et une explosion des coûts titanesque … totalement le contraire de l’objectif initial !
La solution TopSolid Integrated Digital Factory, suite logicielle de CFAO et de gestion communiquant, permet justement de s’affranchir de ces contraintes en se reposant sur :
- un système intégré et modulaire qui prend en compte l’ensemble des besoins de l’entreprise
- la numérisation de toute la chaîne de valeur de la prise de commande à la livraison, à travers la suite logicielle TopSolid
Du chiffrage d’un projet au contrôle qualité, voici le tour d’horizon des avantages du logiciel de CFAO et de gestion communiquant TopSolid :
Gestion centralisée de la production : interopérabilité des modules ERP et PDM de TopSolid
L’ERP centralise la gestion globale de l’entreprise et intègre nativement les modules ordonnancement, GED, qualité, GPAO et le pilotage d’atelier, en interconnexion avec le PDM TopSolid, qui gère, trace et sécurise en temps réel les données CFAO. Cette structure permet de maîtriser les processus de conception/simulation/fabrication de l’ensemble des métiers adressés, grâce à la traçabilité des révisions, au partage de données et à la collaboration. De fait, le processus de gestion de production est plus agile, le gain de temps est considérable et la productivité augmente.
Gestion des commandes et chiffrage des projets avec le module intégré TopSolid’PartCosting
Le module chiffrage des projets de TopSolid Integrated Digital Factory est entièrement paramétrable et commun à tous les intervenants. Les deviseurs bénéficient d’un package d’atouts très appréciable :
- Choix de la méthode de chiffrage avec systèmes d’assistance
- Utilisation directe du plan de pièce 2D ou 3D
- Calcul rapide et fiable des temps et des coûts d’usinage
- Devis technique précis permettant une maîtrise des marges de négociation
Conception des assemblages, programmation des pièces et simulation avec les modules CFAO intégrés
Cette brique de l’Integrated Digital Factory représente une aubaine pour les Bureaux d’Etudes : conception de pièces unitaires, pièces et assemblages complets, simulation de mécanismes complexes, dossiers de production correspondants (nomenclatures, plans de détail, plans d’ensembles) … Le logiciel communicant nativement avec le PDM, l’ERP et les outils standard CFAO le processus de conception est accéléré et plus efficace !
La suite logicielle intègre également la solution de fabrication modulaire et flexible TopSolid’Cam, pour programmer des pièces en fraisage, tournage, fraisage/tournage, décolletage et tous types d’usinage, en fonction des spécificités machines et de certaines pièces, ainsi que des besoins des clients.
La simulation du comportement de la machine par rapport au résultat FAO (code iso), part importante du processus de fabrication, bénéficie des meilleures fonctionnalités de l’extension TopSolid’CamSimul : réplique numérique intégrale de la machine réelle, simulation de tours complexes, détection des collisions et vérification des conditions de coupe en temps réel et optimisation des programme existants.
Au final, la combinaison temps d’usinage, sécurité, qualité est toujours optimale.
Gestion des ressources atelier plus fine et meilleure organisation de la production
Machine CN, bancs de mesure, réserve d’outils simples ou assemblés, outillage, outils coupants, robots, dispositifs de stockage connectés … les ressources de l’atelier et les flux de données qui y sont liés sont nombreux et tendent même à se multiplier. La suite TopSolid Integrated Digital Factory en facilite la gestion, grâce à l’intégration parfaite des données FAO, elles-mêmes interfacées en temps réel avec le PDM.
Résultat : collaboration efficace avec l’atelier, coûts annexes supprimés, et gain de productivité au Bureau des Méthodes avéré !
Automatisation du processus de contrôle de la qualité
Terminée la saisie manuelle des plans de contrôle : toutes les étapes du processus sont automatisées, qu’elles concernent le Bureau des Méthodes, la salle de contrôle ou la sortie de machine. Dématérialisation, traçabilité, limitation des erreurs et gain de temps : cette dernière brique termine la chaîne TopSolid Integrated Factory sur une note additionnelle de hausse de performance industrielle.
Conclusion
Pour allier efficacité et qualité, la continuité numérique sur l’ensemble de la chaîne de valeur est incontournable. La suite TopSolid Integrated Factory offrant une vision 360° de la chaîne de conception et fabrication, constitue à ce titre la meilleure réponse du marché. Alliant ergonomie, fiabilité et technologies de pointe, la solution propose diverses manières d’automatiser et rationnaliser votre production, contribuant ainsi à une hausse substantielle de la productivité. TOPSOLID SAS vous accompagne dans la mise en œuvre de votre outil et dans la pérennisation de votre transition numérique.
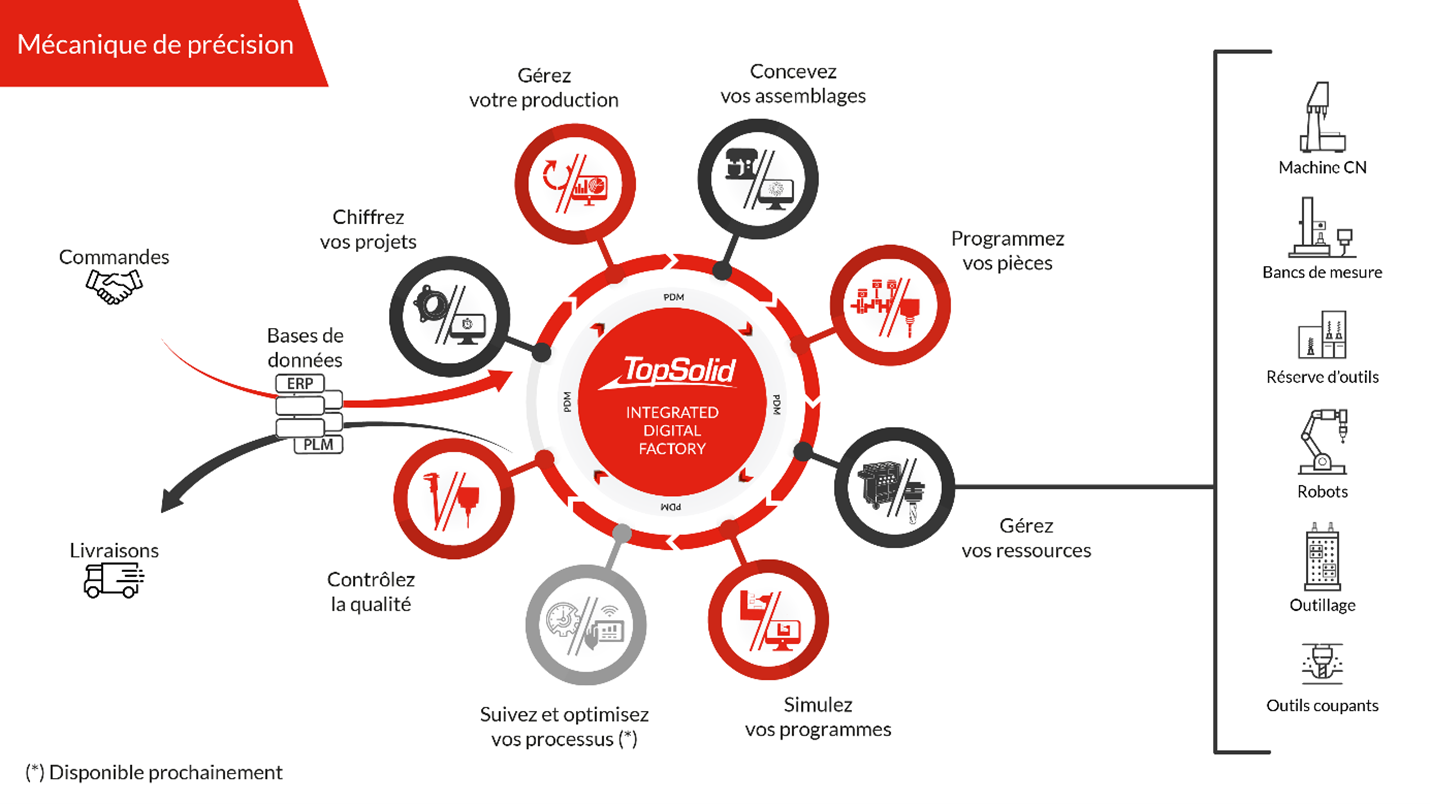