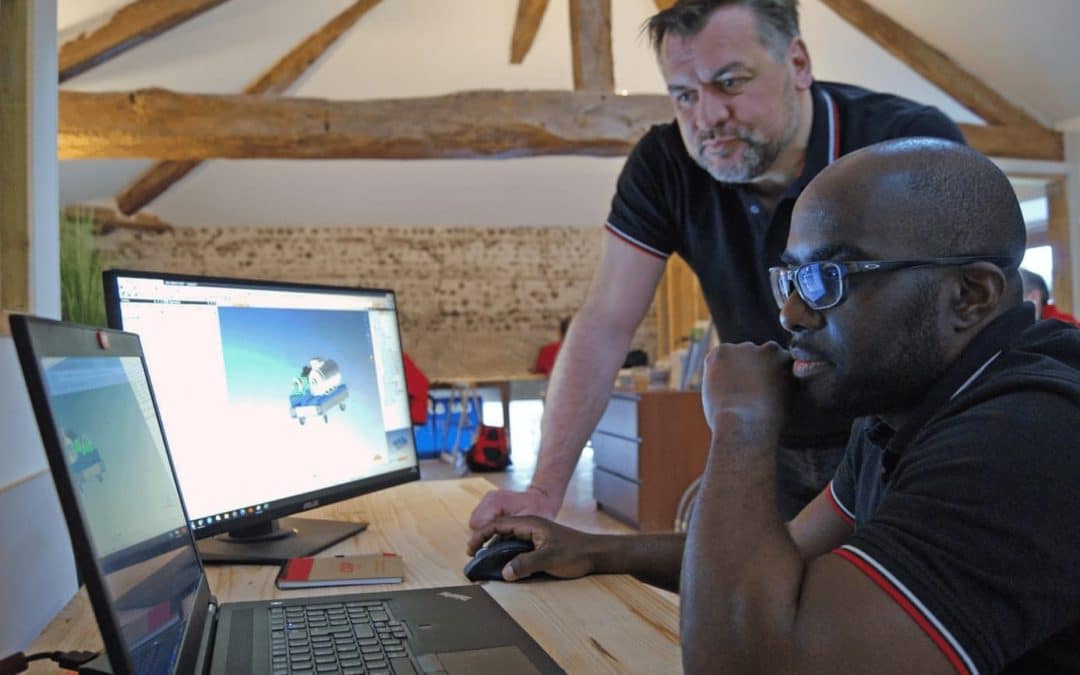
Et si votre CAO était obsolète ? Lumière sur les alternatives dans l’air du temps
C’est un fait : de nombreux bureaux d’études dépendent d’un logiciel de CAO – souvent le même, leader de sa génération. Pourtant, l’évolution des attentes est telle que son utilisation est souvent couplée à celle d’autres outils afin d’obtenir un panel de solutions à la fois varié et complet… mais chronophage et risqué. D’où l’apparition d’alternatives crédibles et plus adaptées aux besoins actuels. TopSolid vous donne les clés pour une transition en douceur – et réussie.
Quand le monopole a ses limites
Si les solutions de CAO traditionnelles constituent souvent une zone de confort pour leurs utilisateurs, ces derniers sont pourtant régulièrement confrontés à leurs limites :
- des fonctionnalités peu évolutives malgré des mises à jour régulières,
- des coûts cachés directs et indirects élevés pour l’acquisition, la prise en main et la maintenance,
- un Product Data Management (PDM) entravé,
- une incompatibilité avec les modes de travail actuels (utilisation collaborative et multi-sites, entre autres),
- un manque d’adaptabilité aux métiers spécifiques et émergents.
Tous ces freins annoncent l’obsolescence de ces outils malgré un ancrage fort au sein des bureaux d’études. Il devient donc urgent de se pencher sur le déploiement d’une solution permettant de maintenir l’activité à flot, grâce à un processus optimisé, c’est-à-dire fluide, collaboratif, moderne et économique.
Panorama des alternatives crédibles sur le marché de la CAO
Fort heureusement, le marché des solutions de CAO s’est diversifié pour répondre à des pratiques variées et à des attentes croissantes. Aujourd’hui, il est donc possible de choisir entre une solution connectée et portative grâce à sa synchronisation sur le cloud, et une solution locale, généraliste ou spécialisée. Le tout, avec une offre tarifaire variable afin de couvrir tous les besoins… et tous les budgets.
Cette diversité de choix impose toutefois une condition pour avancer le plus efficacement possible dans votre prise de décision et votre transition : il devient essentiel de définir précisément vos critères. Votre mission, en amont, est donc de passer en revue et de désigner vos attentes en matière de prise en main, de PDM, de capacités collaboratives et de spécialisation métier, entre autres.
La gamme de solutions CAO, FAO, ERP TopSolid
TopSolid : une réponse française aux défis contemporains
Développé en France par une équipe d’experts proches de ses utilisateurs, TopSolid assure une réponse rapide à vos besoins d’évolution et de support. L’outil, qui s’inscrit dans la lignée des logiciels de CAO, combine plusieurs fonctionnalités largement plébiscitées :
- un paramétrage personnalisé,
- un PDM natif et collaboratif intégré,
- des fonctionnalités métier avancées,
- des outils spécialisés pour différentes pratiques (usinage, tôlerie, mécanique, etc.),
- une intégration dans votre écosystème même à l’international.
En comparaison avec les outils de CAO ancrés dans les mœurs, TopSolid, en tant que solution entièrement intégrée, vous épargne par ailleurs des dépenses supplémentaires qui peuvent peser lourdement sur votre budget. Et ce, grâce à la réduction des coûts directs et indirects (abonnements, maintenance, options supplémentaires, etc.).
Par extension, grâce à une conception la plus complète possible et pensée pour la collaboration, la solution se met au service de votre productivité, favorisant un retour sur investissement considérable.
Enfin, nous vous avons gardé le meilleur pour la fin : là où les solutions traditionnelles se font souvent reprocher leur manque d’évolution, TopSolid se veut être un outil évolutif avec des mises à jour régulières et sans impact sur son coût.
Comment réussir la transition de votre outil de CAO vers TopSolid ?
Bien entendu, une telle évolution dans vos processus se prépare avec minutie. Si les équipes de TopSolid sont sur le pont pour vous accompagner du déploiement à l’utilisation en passant par la prise en main, vous devrez également évaluer et anticiper vos besoins en toute objectivité.
Cette introspection repose sur un audit de vos processus existants, une identification claire des points d’amélioration, et une projection à moyen terme.
Dans un second temps, TopSolid vous propose de tester la solution pour vous rendre compte de son ergonomie, de ses performances et donc de son potentiel pour votre bureau d’études. Et pour cause, un test réalisé sur un projet concret permet de :
- lever un certain nombre de doutes,
- conserver une coexistence temporaire en phase de rodage,
- et déployer la solution à plus grande échelle en toute sérénité.
Enfin, si vous décidez de franchir le pas, souvenez-vous que nos équipes développent la solution avec pédagogie. Vous pourrez donc compter sur leur formation et leur support technique, qui limitent les risques et garantissent une transition en douceur.
La CAO occupe une place prépondérante dans les bureaux d’études. Choisir une solution adaptée à vos pratiques, à vos besoins et aux projets de vos clients apparaît essentiel dans ce contexte.
En optant pour une solution complète, polyvalente et sécurisée, vous gagnerez sur tous les plans : productivité, fiabilité et rentabilité. Un ensemble de qualités portées par TopSolid, que vous pourriez tester très prochainement en demandant une démo.