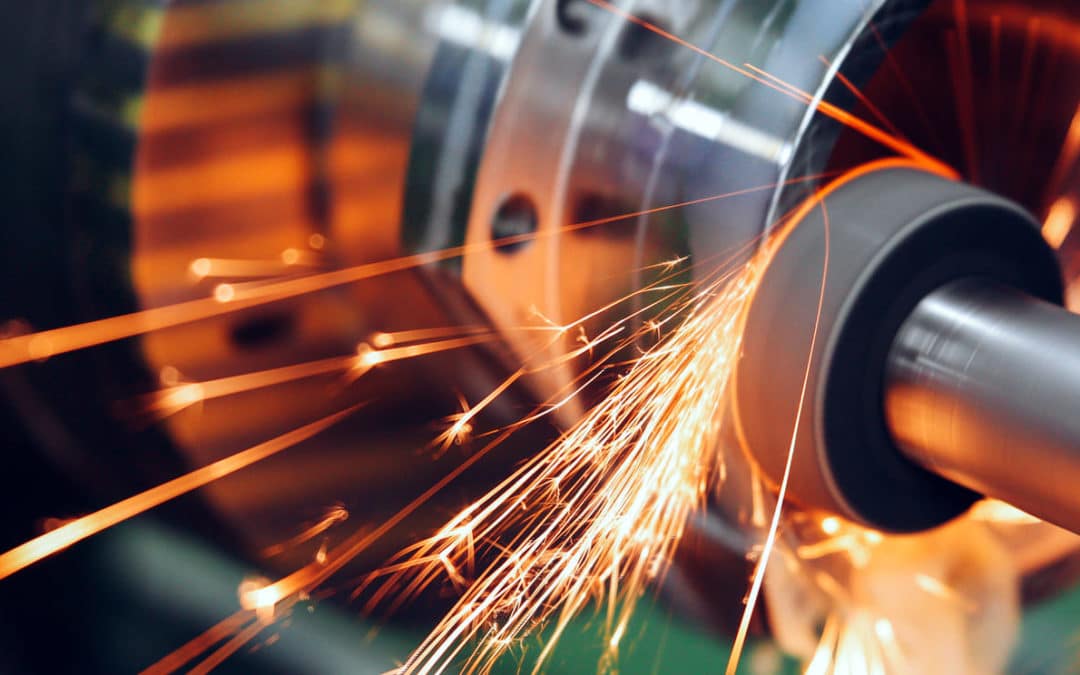
CAD/CAM for grinding on your machine tools
More precise than traditional machining operations, grinding enables the surface of a product to be finely modified thanks to the abrasive machining technique. Nevertheless, investing in the right machine tools to perform this type of operation represents a significant cost for companies, more so as their piloting can prove difficult for programmers. To facilitate grinding on these machine tools, some manufacturers are exploring the possibilities offered by CAD/CAM. But what additional advantages does CAD/CAM offer this activity? Here’s how.
The challenges of rectification
By employing the principle of abrasive machining, grinding achieves exceptionally high dimensional accuracy on parts, enabling us to meet customer requirements better. Whereas traditional machining operations involve the removal of a swarf, grinding acts more finely on the material, polishing it with a grinding wheel.
While the effectiveness of this method is not in doubt, it nevertheless represents a significant investment for companies: they must purchase the machine tools required for these operations. The challenge for organizations is to measure the profitability of the proposed solutions. To carry out grinding operations, they can:
- Either invest in grinding machines dedicated exclusively to honing.
- Or to invest in combined machines for both machining and grinding.
The limits of “foot-in-the-machine” programming
In the first case, i.e., with a solution that combines machining and grinding, companies can adapt and create grinding programs for the machine.
The disadvantages of this approach are manifold:
- Lack of flexibility: unlike CAM, this programming does not allow machine simulation and collision checks.
- High cost: this type of programming requires the purchase of a grinding machine in addition to the machine tool, plus handling costs.
- Risk of inaccuracy: Moving parts from the machine tool to the grinding machine amplifies the risk of inaccuracy.
- Considerable programming time: programming machine tools and setting up grinding machines can be time-consuming for the teams in charge.
The range of CAD, CAM, ERP and PDM TopSolid solutions
CAD/CAM to optimize grinding on machine tools
Faced with these limitations, some manufacturers have developed combined machines which, thanks to CAD/CAM, allow:
- First, machine a part by milling and turning.
- Grind the same part in a second step.
The part does not need to be moved, as all handling is done on the same machine. This eliminates repositioning errors caused by moving the part from the machining center to the grinding machine and saves valuable handling time.
Point of attention: the need for a dedicated grinding CAD/CAM tool
For companies equipped with machines that combine machining and grinding, choosing the right CAD/CAM software is crucial. Only some CAD/CAM solutions contain dedicated grinding operations; some propose diverting machining operations into grinding operations. This is not a very relevant approach, as the method used to pilot a grinding wheel differs significantly from that used in milling or turning.
This type of solution offers no added value to the programmer, who is forced to manually adjust the ISO code to obtain the correct surface finish on the part. This is why companies are strongly advised to opt for a CAD/CAM tool that has specifically designed the grinding operation.
TopSolid’Cam: a software designed to optimize grinding on machine tools
TopSolid’Cam is a complete, high-performance CAD/CAM software package that supports and facilitates the design work of programmers thanks to:
- Easy and complete solution integration.
- Interoperability with all CAD software.
- A self-managed working environment.
- Production optimization thanks to a duplication process.
- Different simulation levels.
- Change management and tracking.
- An answer to a wide range of milling and machining needs.
More specifically, TopSolid’Cam’s “grinding on machining center” functionality enables customers equipped with machine tools to combine machining and grinding to optimize the management of this operation. Indeed, the solution offers the possibility of programming the grinding process directly from the software, even before the part is mounted on the machine. Designed explicitly for on-machine grinding, this functionality adapts to the characteristics of each operation and facilitates the programmer’s work.
Would you like to learn more about TopSolid’s machining center grinding functionality? Ask our team for a demonstration.