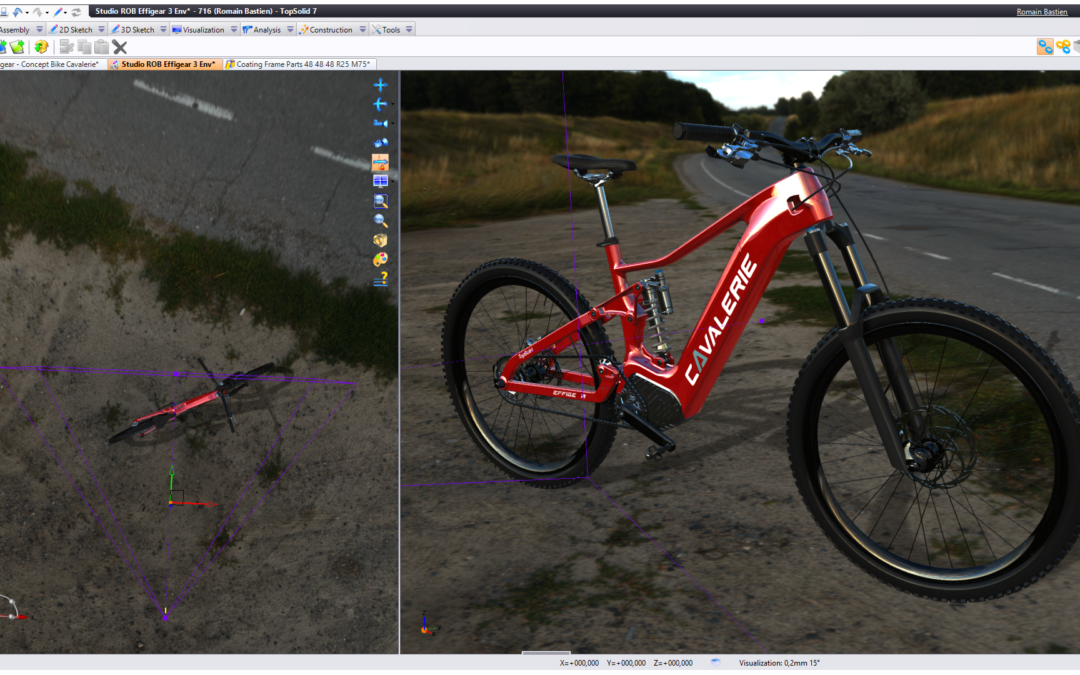
Modélisation 3D : tout ce qu’il faut savoir !
© Effigear
Pensez à un cube. Bravo ! Vous venez de faire de la modélisation 3D. Devenue populaire dans les années 1990, cette technique permet de créer des représentations virtuelles tridimensionnelles d’objets, de bâtiments, de personnages et bien plus encore. Elle joue un rôle essentiel dans de nombreux domaines tels que l’architecture, le design industriel, l’animation, les jeux vidéo et même la mode. Selon Fortune Business Insights, le marché de la cartographie et de la modélisation 3D était estimé à 6,77 milliards USD en 2024 et devrait atteindre 7,60 milliards USD en 2025, avec un taux de croissance annuel moyen de 16,5 %.
Qu’est-ce que la modélisation 3D ?
Pour donner une définition un peu précise, la modélisation 3D est « le processus de création d’objets tridimensionnels virtuels à l’aide d’un logiciel dédié ». Elle permet de représenter des objets de manière réaliste en ajoutant des détails, des textures, des couleurs et des propriétés physiques.
Les modèles 3D peuvent être créés à partir de zéro ou en utilisant des techniques de numérisation 3D pour capturer des objets réels. Ces modèles peuvent être visualisés sous différents angles et échelles, ce qui facilite l’analyse, la conception et la communication des idées.
La modélisation 3D pourrait être décrite comme la création d’un monde virtuel en trois dimensions dans lequel des objets prennent vie grâce à des formes et des textures réalistes. C’est comme si l’on façonnait un univers imaginaire à partir de blocs de construction numériques, où chaque élément peut être manipulé et observé sous tous les angles.
La modélisation 3D est un moyen de donner forme à l’imagination, de matérialiser des idées abstraites et de les rendre tangibles dans un espace virtuel. Vous créez un paysage mental en utilisant des outils numériques pour sculpter et façonner des formes qui existent seulement dans votre esprit, et vous pouvez les partager avec d’autres, qui peuvent à leur tour les explorer.
La modélisation 3D est une fenêtre ouverte vers des possibilités infinies, où la créativité peut s’épanouir et où les mondes numériques prennent vie.
Dans quels domaines la modélisation 3D est-elle utile, et pour quoi faire ?
La modélisation 3D est utilisée dans de nombreux domaines. Les plus connus sont l’architecture, le design industriel, l’animation et les effets spéciaux, les jeux vidéo, ou encore l’ingénierie :
- Architecture : Les architectes utilisent la modélisation 3D pour créer des représentations virtuelles réalistes de bâtiments et de structures, permettant une meilleure visualisation et une meilleure communication des concepts architecturaux.
- Design industriel : essentielle dans le processus de conception de produits, la modélisation 3D permet aux concepteurs de créer des prototypes virtuels, d’effectuer des tests et des simulations avant la production réelle.
- Animation et effets spéciaux : Dans l’industrie du cinéma et de l’animation, la modélisation 3D est utilisée pour créer des personnages, des décors et des effets spéciaux époustouflants. De plus en plus époustouflants !
- Jeux vidéo : Les développeurs de jeux vidéo utilisent la modélisation 3D pour créer des mondes virtuels immersifs, des personnages et des objets interactifs.
- Ingénierie : La modélisation 3D est également utilisée dans l’ingénierie pour concevoir des pièces, des machines et des systèmes complexes, permettant de détecter les erreurs de conception et d’optimiser les performances avant la fabrication.
- Marketing et publicité : L’imagerie 3D est utilisée dans les campagnes publicitaires pour présenter des produits de manière attrayante et réaliste. Les rendus 3D permettent de montrer les caractéristiques et les fonctionnalités d’un produit de façon plus immersive et convaincante.
- Impression 3D : La modélisation 3D est étroitement liée à l’impression 3D. Les modèles 3D sont en effet utilisés comme base pour créer des objets physiques à l’aide d’imprimantes 3D. Les logiciels de modélisation 3D permettent de concevoir et de préparer les fichiers nécessaires à l’impression des objets souhaité.
La gamme de solutions CAO, FAO, ERP TopSolid
Quels sont les avantages de la modélisation 3D ?
Pouvoir visualiser un objet, une forme, un personnage, un paysage, en trois dimensions, ça paraît tout de suite très ludique. Parlez-en à vos enfants ! Mais c’est bien plus que cela. Les intérêts très concrets à faire de la modélisation 3D sont nombreux :
- Simplification du processus de conception : Grâce à l’utilisation de logiciels avancés (CAO 3D notamment), la modélisation 3D permet de simplifier le processus de conception.
- Visualisation et simulation : La modélisation 3D est utilisée dans des domaines tels que le cinéma, la télévision, les jeux vidéo, l’architecture, la construction, le développement de produits, la science et la médecine pour visualiser, simuler et obtenir le rendu des conceptions. Elle permet de créer des modèles tridimensionnels réalistes et facilite la communication des idées.
- Précision et qualité : Les rendus en 3D offrent une meilleure qualité et précision par rapport aux rendus en 2 D. La modélisation 3D permet de créer des perspectives réelles et facilite l’interprétation des projets, tant pour les professionnels que pour les novices.
- Réduction des coûts : La modélisation 3D peut contribuer à la réduction des coûts dans le processus de conception. En offrant une meilleure visualisation et simulation des projets, elle permet d’identifier les erreurs ou les problèmes potentiels plus tôt, évitant ainsi des coûts de correction ultérieurs.
- Accélération du développement de produits : L’impression 3D, qui est une application de la modélisation 3D, permet de créer des prototypes plus rapidement et efficacement. Cette technologie facilite le passage de la conception à la réalisation physique, ce qui est particulièrement avantageux pour le développement de produits.
- Facilitation de la communication : La modélisation 3D en réalité virtuelle (VR) offre de nouveaux moyens de communiquer des idées et de présenter des projets. Elle permet une immersion plus réaliste et interactive, donnant ainsi une meilleure compréhension et une expérience plus engageante.
- Amélioration de la collaboration : La modélisation 3D facilite la collaboration entre les différents acteurs d’un projet. Les modèles tridimensionnels permettent une meilleure compréhension et coordination entre les équipes, ce qui favorise la collaboration et réduit les erreurs de communication.
Quels outils permettent de faire de la modélisation 3D ?
Vous aimeriez faire de la modélisation 3D, mais ne savez pas quel logiciel choisir ? Voici les plus connus :
- TopSolid : La modélisation 3D est au cœur des logiciels de CAO TopSolid. Ils intègrent des outils de modélisation solides et surfaciques, permettant de créer des pièces complexes et d’exprimer sa créativité. Ses nombreuses fonctionnalités conçues pour répondre aux besoins de toutes les industries en fait le partenaire idéal pour les bureaux d’étude.
- AutoCAD : Utilisé dans le domaine de l’architecture, de l’ingénierie et de la construction, ce logiciel de modélisation et de dessin 3D offre des fonctionnalités avancées pour la création de modèles 3D précis et détaillé
- SolidWorks : Plutôt destiné aux concepteurs et ingénieurs, SolidWorks est un logiciel de CAO 3D largement utilisé pour créer des modèles 3D, des assemblages et des dessins techniques.
- Blender : Logiciel de modélisation, d’animation et de rendu 3D polyvalent. Il est utilisé dans de nombreux domaines, notamment le cinéma, les jeux vidéo, l’animation et la création artistique.
- SketchUp : Pour l’architecture, le design d’intérieur et la modélisation d’objets. SketchUp permet de créer rapidement des modèles 3D et d’explorer différentes options de conception.
Une fois les modèles 3D réalisés, la visualisation devient essentielle pour tester et présenter efficacement les projets. Des outils comme Weviz, spécialisé dans la visualisation industrielle immersive, ou TopSolid’Virtual, qui propose des expériences interactives en réalité virtuelle, permettent de projeter les modèles dans un environnement réaliste, facilitant la prise de décision et la communication.
Le module TopSolid’Predict va encore plus loin en anticipant les commandes de modélisation grâce à une IA locale, ce qui accélère significativement le travail de conception.
La modélisation 3D ne cesse d’évoluer. Les logiciels deviennent plus intelligents, plus intuitifs, et s’intègrent désormais dans des processus complets de production, de la conception à l’atelier. Grâce à la réalité virtuelle et à l’intelligence artificielle, les professionnels gagnent en efficacité, en réactivité et en qualité.
Et pour tirer le meilleur parti de ces outils, il reste essentiel de se former. Découvrez comment monter en compétence ou faire évoluer vos équipes avec nos formations CAO.