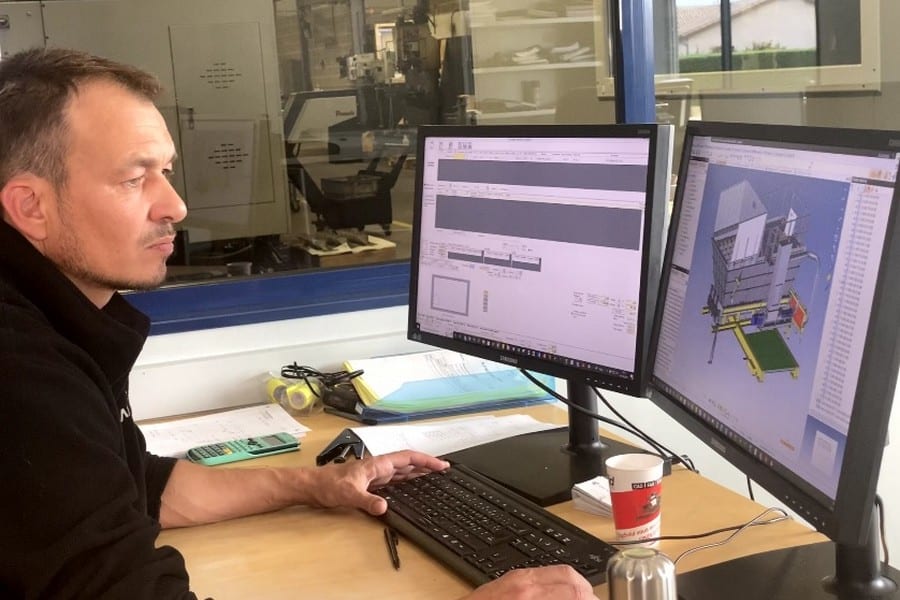
Success Story : TopSolid by Rabumeca
Etablie dans le département de l’Ain, l’entreprise Rabumeca élabore et fabrique des ensembles mécano-soudés en acier, inox et aluminium pour différents secteurs. Créée en 1989, la société justifie de nombreuses années d’expérience dans son domaine, qui lui ont notamment valu d’obtenir le prix « qualité, coût, délai » décerné par ArcelorMittal en 2013. En pleine expansion, Rabumeca a intégré depuis 2020 le logiciel TopSolid’Design à sa conception. Rencontre avec Sébastien Bridet, gérant de l’entreprise Rabumeca.
Expérience, savoir-faire et conviction : la recette d’une entreprise qui marche
Portée par plus de vingt ans d’expérience, la société Rabumeca s’est peu à peu déployée dans les secteurs de l’agroalimentaire, la pharmaceutique, la sidérurgie et l’environnement. Aujourd’hui elle compte 20 salariés et comptabilise un chiffre d’affaires de 2,7 millions d’euros en 2021. Au cœur de son projet, on retrouve la détermination d’offrir des services de qualité qui respectent des délais déterminés et la volonté d’établir une relation de confiance avec ses clients et ses partenaires commerciaux.
Le déploiement de Rabumeca dans différents secteurs industriels a permis aux collaborateurs de l’entreprise de développer des compétences techniques variées. Au fil des années, l’entreprise gérée par Sébastien Bridet a également développé son expertise via une politique d’investissements, visant à améliorer la fiabilité et la performance des équipements. Dans cette optique, la collaboration avec TOPSOLID s’est faite tout naturellement.
Rabumeca et TOPSOLID : une histoire récente
Nécessitant un nouveau logiciel de CAO pour augmenter sa productivité, Rabumeca a lancé un appel d’offres en 2020. Pour l’entreprise, le choix de TOPSOLID a été évident : « Nous avons retenu TopSolid car ce sont les seuls qui ont su nous comprendre et écouter notre besoin. Nous avons eu des interlocuteurs qui étaient du métier et qui ont su adapter leur logiciel de dessin à notre processus de fabrication », relate ainsi Sébastien Bridet.
En application, les collaborateurs utilisent TopSolid’Design pour le lancement en fabrication et la conception de produits en machines spéciales. Nicolas Laibe, chargé d’affaires chez Rabumeca détaille le processus : « J’utilise TopSolid’Design pour récupérer les fichiers 3D des clients et donner les renseignements techniques nécessaires au projet. J’utilise les modules de reconnaissance de tôles et de tubes et j’obtiens les documents nécessaires à la fabrication. » Le logiciel lui permet ainsi de construire « tout ce qui est mise à plat pour le laser, fiche de pliage, les plans de montage par sous-ensembles, les plans d’ensembles avec toute la nomenclature correspondante. »
TopSolid’Design au service du développement de Rabumeca
Logiciel de CFAO spécialisé, TopSolid’Design accompagne les projets de Rabumeca avec efficacité. Véritable outil de productivité, les équipes apprécient notamment sa facilité d’utilisation.
Un accompagnement sur l’ensemble du processus
Rabumeca a trouvé en TOPSOLID un interlocuteur pédagogue qui a su guider les collaborateurs de l’entreprise dans la prise en main du logiciel : « Nous avons eu une formation de TopSolid’Design de 6 jours au siège de TOPSOLID et nous avons eu une formation spécifique dans nos locaux, adaptée à nos besoins », explique Sébastien Bridget. Selon lui, c’est la qualité des accompagnateurs qui a fait la différence : « Nous avons trouvé des personnes en face de nous qui répondaient quotidiennement à nos besoins, à nos questionnements et qui ont su nous accompagner tout au long de la mise en place du logiciel. »
Une facilité d’utilisation
Pour les chargés d’affaires, TopSolid’Design représente une valeur ajoutée à la création, notamment en termes de facilité d’utilisation. C’est en tout cas ce que dévoile Nicolas Laibe : « Je trouve TopSolid’Design très facile d’utilisation, il nous aide à avoir les bons documents. C’est logique, c’est clair, il y a les bonnes icônes et les bonnes fonctionnalités. Cela reprend bien l’utilisation que l’on a en atelier. »
Un gain de productivité
Plus globalement, c’est un véritable essor de productivité que l’entreprise a constaté grâce à TopSolid’Design. Avec plus d’un an de recul, le gérant de Rabumeca raconte : « TopSolid nous a permis d’automatiser toutes les tâches que l’on faisait manuellement. Les documents de travail nous ont permis de gagner énormément de temps lors du lancement de nos process. » Selon lui, les gains en productivité gagnés par l’entreprise grâce au logiciel sont donc loin d’être négligeables : « On estime avoir gagné environ 30% de productivité sur le poste méthode », affirme-t-il.
La gamme de solutions CAO, FAO, PDM et ERP TopSolid
Des perspectives de développement étroitement liées à TOPSOLID
Pour Rabumeca, l’objectif dans un avenir proche c’est de développer ses fonctionnalités pour répondre encore mieux aux besoins de ses clients. Dans cette optique, Sébastien Bridget souhaite intégrer le module devis de TopSolid à son organisation. Par une mise en place de systèmes facilitateurs, ce module permet notamment, via un plan de pièce 2D ou 3D d’obtenir un résultat proche de la réalité de l’atelier. Fière de leur parcours, TOPSOLID se fera encore une fois un plaisir de les accompagner dans cette démarche !