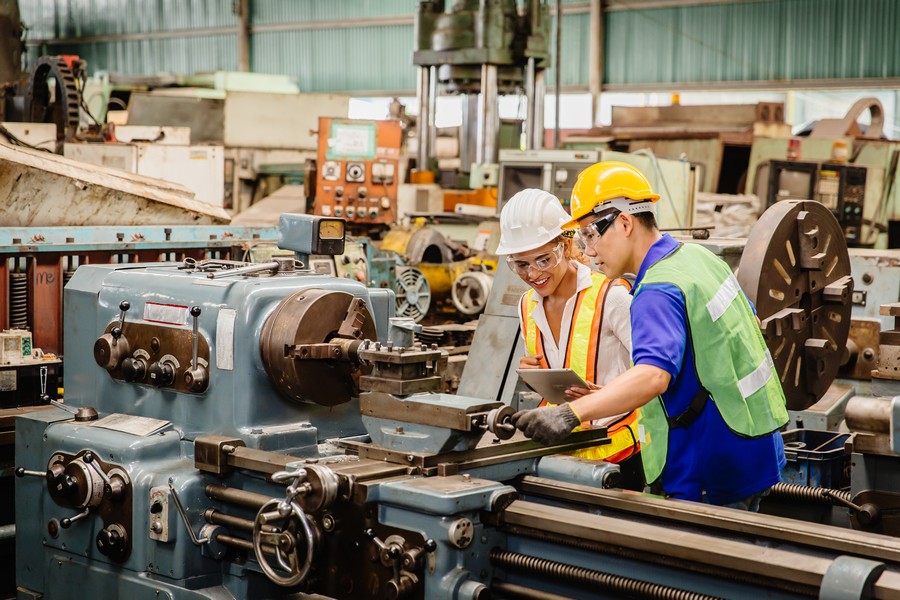
Making tool management simple – Is it possible?
If producing machined parts for your manufacturing tools is a complex process, should the system that is supposed to make it more efficient be a “necessary evil”? Considering the cost of stopping production because a part is missing from the tool magazine, the necessity of a good tool management system seems obvious, but it does not have to be complicated as it should be designed to make your processes more efficient and safer. Here is how.
1) “Tool Management”: what do we mean by that?
Tool management encompasses physical tool management in a workshop as well as all the technical data attached to each tool and component used in your manufacturing process. This is usually handled by a dedicated software designed to assist machine parts manufacturing by automatically loading technical data into the CAD/CAM system as well as managing tools’ and components’ physical inventory.
Tool management becomes even more important when considering next-generation CAD/CAM software. Based on 3D modeling, machine kinematics, advanced simulation and many other tools needed to create high-precision machined parts, a lot of data is generated to ensure that the products coming off your assembly lines are of the highest quality.
This data needs to be accurate, up-to-date, available, and ready to be retrieved. This way, you avoid inaccuracies and save time and money in the overall process, which also means improving profits.
2) Challenges that come with tool management
Since tools and components for manufacturing processes are a very large and complex topic, one of the biggest challenges is the interface to get the 3D data into the CAD/CAM application. Indeed, in addition to the 3D graphic, a tool also contains many parameters and functions in space that form the basis of the toolpath algorithm in CAM. If there is a single faulty parameter, the operation in CAM is invalid and cannot be generated.
Another challenge is that most of the available solutions on the market only work by pure database application, which means that you only get a graphic view (and not a 3D visualization) of the part to be produced. This makes it confusing and complicated to use, especially for occasional users. Most of these solutions do not facilitate 3D data management or even offer a functional interface for CAM applications.
3) The benefits of a good tool management solution
If all the data for each tool and component are centrally managed, any information can be retrieved at any time and from anywhere in the company. In addition, good tool management ensures that all references and back references are stored, not only for transmission to the CAM system, but also for all existing NC programs. This allows you to better plan for new programs as well as improve change management.
A good tool management solution also provides you with a real time picture of your tool magazine on the shop floor, allowing you to directly synchronize your machine magazine with your CAM environment. Therefore, by centralizing production data, you can optimize your workshop organization and increase overall productivity by:
· Reducing machine set-up lead time
· Improving traceability of program modifications
· Providing precise tool location
· Monitoring the use and wear of tools
4) Advice for beginners
If you are thinking about implementing a tool management system, you should look for a solution that will help you to efficiently manage your tool components, your assembled tools, their life cycle, and is running on a single data source that is always easily and readily accessible. But above all, it should be adapted to your activity!
The tool management solution you consider should be able to adapt to your existing processes, workflows, and growth strategy by being completely modular and scalable. Think big in order to be able to implement additional modules in the future!
You should also be able to build on your existing NC data. As you are not starting from scratch, your tool management solution should automatically take into account your existing data in an intelligent way. Indeed, you cannot afford to stop production while you fill in and set up the database. The system must be able to connect existing data, learn and expand while using it, and integrate it step by step.
5) Why TopSolid’ShopFloor can answer your needs in terms of tool management
What makes TopSolid really unique on the market is that there is no interface between the tool management system and the CAM application. TopSolid’ShopFloor is a product that is completely based on TopSolid’PDM as are all TopSolid solutions. Thus, components and tools are controlled by revision, oriented towards properties and BOMs like a “standard” part or assembly and are fully associable with all modules available in TopSolid (CAM, Design, Draft, …).
To easily create components and assemblies, TopSolid provides libraries to create your own components from fully parameterized ISO 13399 models. Of course, you can also import and use supplier data. TopSolid’ShopFloor supports all data, even data from other tool management systems.
Searching for components and creating assemblies are simple and can be managed via TopSolid’ShopFloor Tool Manager. The fully graphical drag and drop assembly process is very user friendly and is a great help in daily activities.
In other words, a system that:
- has no interface
- does not translate or transform any data to create the toolpath
- builds the data source on the TopSolid core
We can 100% guarantee that a tool defined in the TopSolid environment is functional throughout the process, from CAM to presetting and machining.
TOPSOLID is a leading CAD/CAM software company in the world. With more than 35 years of experience, we are able to offer fully integrated CAD/CAM solutions adapted to your industry, whether it is in mechanics (machines, tools, etc.), sheet metal or wood industry. Wherever a machine interacts with the material to be machined, whether to shape or produce a part, we have an adapted, innovative, and unique solution. To learn more, contact us!