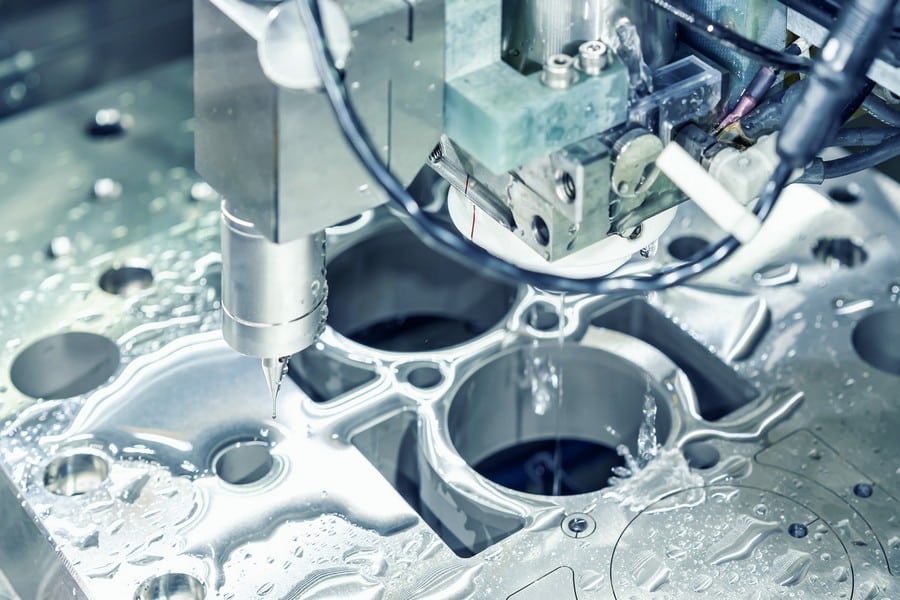
Your complete guide to machining
The definition of machining
What does machining mean?
Machining is a manufacturing process that consists of shaping a rough material, such as metal, plastic or wood, by removing material to make a finished part with precise dimensions and specific characteristics. Machining is one of the most widely-used methods used in industry, from automotive and aerospace, to energy and electronics.
The main goal of machining is to create complex shapes and finished surfaces with a high degree of precision. This can include the creation of cavities, grooves, threads, drill holes, flat surfaces or curves, according to the technical specifications of the end product.
One of the main advantages of machining is its versatility. Machining can be used to produce a broad range of parts, from simple individual components, to more complex assemblies. In addition, machining is well adapted to different types of materials, in particular ferrous and non-ferrous metals, technical plastics and composites.
Close-up on the machines
The machining process involves the use of a machine tool, such as a lathe, a milling machine, a grinding machine or a drill, which is precisely controlled to progressively and methodically remove the material. Different cutting tools, such as drills, milling cutters, reamers and blades are used, according to the specific needs of the machining operation.
Machining has evolved over the years, with the introduction of new technologies and techniques. Modern machine tools have become increasingly automated, featuring numerical control systems and advanced sensors that improve the precision, productivity and safety of machining operations. These days, most companies use numerically controlled machine tools, in combination with a computerized system (CAM), that partially or totally automates the machining procedure.
What is a machining technician?
A machining technician is a qualified professional, specialized in the execution of machining operations. They are responsible for the preparation and installation of the machine tools, the choice of the right cutting tools, the adjustment of the cutting parameters and the execution of the machining operations. To do this, they must be capable of understanding and interpreting technical drawings, selecting the right machining methods for the specifications and using the machines and measuring instruments with precision in order to guarantee conformity with the required tolerances.
In addition to their technical skills, machining technicians must have a sound understanding of the materials, the machining processes and safety standards. They must be capable of analyzing potential problems, solving manufacturing defects and taking corrective measures to guarantee the quality of the machined parts. With the rapid evolution of the machining industry, machining technicians must keep up to date with the new technologies and progress in the field. They may have to work on advanced machine tools, integrate numerical control systems and use computer-assisted design (CAD) software to optimize the machining processes.
What are the four basic machining operations? Turning
This technique uses a lathe to produce cylindrical, conical or complex-shaped parts, such as threads or grooves. The part to be machined is fixed on a rotating spindle, while the cutting tool moves along the part to remove material and produce the required shape.
Milling
Milling consists of using a rotary milling machine to remove material and create complex shapes, such as grooves, flat surfaces, pockets or contours. Milling machines can be used for 2D or 3D machining, depending on the movements of the part and the cutting tool.
Note that the milling of flat surfaces consists of using a special milling tool to produce smooth and precise flat surfaces. The milling of flat surfaces is often used to produce the bearing or reference surfaces of parts.
Drilling / boring / tapping
Drilling consists of making holes in a part with a drill bit. The drill bit turns and penetrates the part, removing material in order to make a hole of a precise diameter and depth. A conventional drill or a more advanced machine tool can be used for drilling operations.
Tapping makes internal threads inside a hole that has already been drilled. The tapping tool cuts thread-shaped grooves inside the hole, so that bolts and other threaded parts can be screwed into the hole.
Finally, boring increases and improves the quality of a hole that has already been drilled in a part. This operation is generally used in order to obtain very precise tolerances, high quality surface finishes or specific dimensions.
Grinding
Grinding is a high-precision machining operation used to produce very smooth surfaces and precise dimensions. This operation consists of using a grinder with abrasive grinding wheels to remove small quantities of material and obtain very strict tolerances.
These machining operations form the basis of numerous other more advanced machining techniques. It is important to choose the right machining operation, according to the specifications of the part to be machined and the required tolerances and geometric characteristics.
The range of CAD, CAM and PDM TopSolid solutions
What is the future of machining?
There are several major trends in the world of machining.
Increased automation
Machining is becoming more and more automated, with the introduction of robots and smart manufacturing systems. Modern machine tools are equipped with advanced sensors, numerical control systems and artificial intelligence technologies that optimize the production processes, improve precision and speed, and reduce human errors.
- See also – “Boost Milling: how to save time in your machining cycles”.
3D printing for machining
3D printing is being used more and more in machining, especially for the production of complex parts. Metallic 3D printing technologies can be used to produce parts with complex internal geometries, thereby reducing the need for additional machining operations. The integration of 3D printing and traditional machining opens up opportunities for more flexible design and manufacturing.
Hybrid additive manufacturing
Hybrid additive manufacturing combines 3D printing with traditional machining. This approach can build parts with complex structures using 3D printing, and then performing machining operations to obtain finished surfaces, precise tolerances or additional functionality.
The integration of artificial intelligence
The use of artificial intelligence (AI) in machining is on the rise. AI can be used to analyze the data from machine tools in real time, optimize the cutting parameters, detect manufacturing defects and improve the overall efficiency of the machining process.
Sustainability and ecological responsibility
In the future, machining will also focus on sustainability and ecological responsibility. Companies will attempt to reduce their environmental footprint by adopting machining techniques that consume less energy, by using recyclable materials and optimizing their processes to reduce waste.
Irrespective of your business, from medical and aerospace, to general or precision mechanics, molds or progressive dies, clock making, optics or welded parts, TopSolid’Cam can meet all your machining needs. Our different modules offer a broad selection of technical solutions to meet your 2D and 3D milling machining requirements, with four of five axes, positioned or continuous, as well as for turning and bar turning. Want to find out more? Then get in touch!