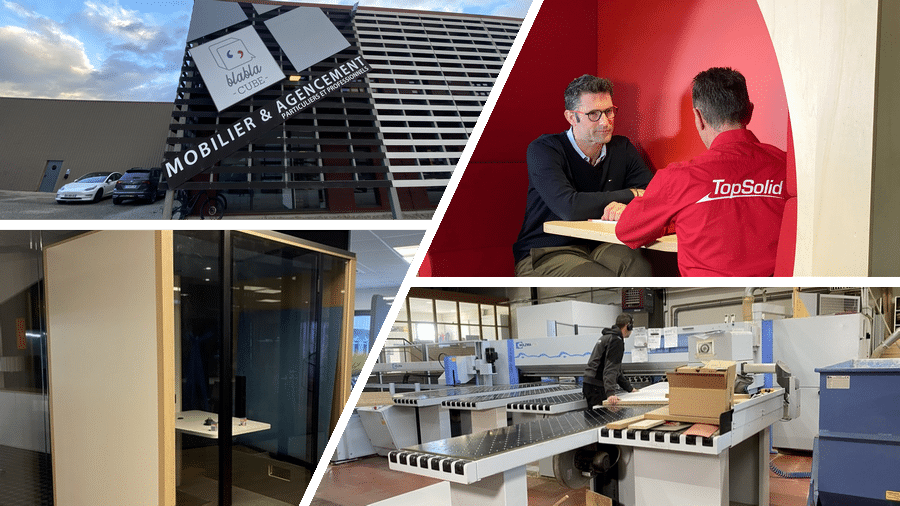
Success Story: TopSolid by Structa
Structa is a 6500 square-foot workshop situated in the heart of the Drôme region, specializing in custom-made furnishings. Since 1981, the company has dedicated its expertise to designing and manufacturing furniture tailored to its customers’ needs. In 2006, they integrated TopSolid’Wood software into its design process to optimize it.
In this interview, we talk with Christian Salomon, CEO of Structa, whom TOPSOLID proudly supports in his projects.
Structa core values: collaboration, transparency, and proximity
Structa is a layout company with around forty staff members, specialized in creating bespoke furniture and fittings for offices, residences, and hotels. The company’s philosophy centers around creative teamwork to best meet customer requirements. Projects are developed collaboratively with the customer from start to finish. Their latest innovation is the design of the Blabla-Cube, a self-contained acoustic pod, designed to create an ideal environment for quiet work.
Structa can boast of having strong values such as networked organization, transparency at all levels, and a commitment to local projects, all underpinned by over four decades of experience. Christian Salomon explains: “We are dedicated to use locally sourced materials. This principle extends to our software choices as well. TOPSOLID is an excellent example: it’s a French software company, based in the Rhône-Alpes region, aligning perfectly with our preference for collaborating with local businesses”.
Structa and CAD/CAM
From design to installation, Structa has consistently upheld its commitment to delivering quality work, leveraging the latest technological innovations in the industry. Since the purchase of its first license in 2006, members of the project and product design departments have been working with TopSolid’Wood software to optimize furniture design and assembly. Fifteen years later, the company, still under the guidance of Christophe Cutillas, a TopSolid’Wood business engineer, has not changed its mind. Christian Salomon cheerfully remarks: “We started with them, and we’re still with them today”.
TopSolid, an added value for Structa’s business
The TopSolid’Wood solution delivers substantial benefits to various Structa departments, from design to production.
Real-time updates for the design office
The members of the design office responsible for designing, cutting, and programming the machines, use TopSolid to manage the export of their projects. The associative solution guarantees that any modification to a project item automatically updates the associated data. “The advantage of TopSolid’Wood is that when you modify something on the original 3D model, our software’s associativity enables real-time alterations and updates in the project.” explains Thomas Levignac, Structa’s design manager. This will undoubtedly enhance the company’s productivity.
Time-saving and increased autonomy in production
The benefits of TopSolid are also visible on the production side. “By using TopSolid in the Production department, we are much more autonomous, we achieve significant time savings when searching for information since the software contains almost all the necessary data” testifies Pierre Vessely, the company’s assembly coordinator. TopSolid facilitates a strong connection between the design and production departments. For example, the software enables fitters to understand in detail the design of a product so that they can assemble it faster and independently.
A major advantage for recruitment
TopSolid also has a role to play in recruitment. “At Structa, we have a lot of apprentices and work-study students” explains Christophe Salomon. “TOPSOLID provides us with temporary licenses for them and more and more newcomers already know TopSolid. It is a huge time saver.”
The range of CAD, CAM, ERP and PDM TopSolid solutions
International development possibilities
Structa has been booming for several years and plans to expand internationally. This is what its CEO hopes: “We will probably set up industrial units abroad to get closer to our foreign customers.”
Structa will logically form a partnership with TOPSOLID to deploy these new industrial units. We look forward to contributing to this exciting project!