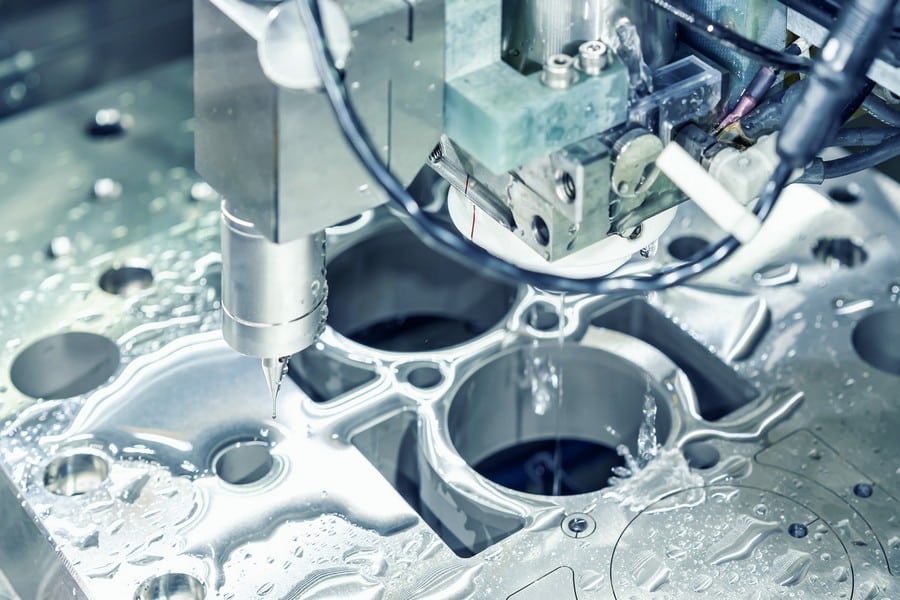
Usinage : votre guide complet !
Usinage : définition
Qu’est-ce que ça veut dire usinage ?
L’usinage est un processus de fabrication qui consiste à donner forme à un matériau brut, tel que le métal, le plastique ou le bois, en enlevant de la matière pour obtenir une pièce finie avec des dimensions précises et des caractéristiques spécifiques. Automobile, aérospatial, énergie, électronique… L’usinage est une des méthodes les plus couramment utilisées dans l’industrie.
L’objectif principal de l’usinage est de créer des formes complexes et des surfaces finies avec une grande précision. Cela peut inclure la réalisation de cavités, de rainures, de filetages, de perçages et de surfaces planes ou courbes, en fonction des spécifications techniques du produit final.
L’une des principaux avantages de l’usinage réside dans sa polyvalence. L’usinage peut en effet être utilisé pour produire une large gamme de pièces, allant des simples composants individuels aux ensembles plus complexes. Par ailleurs, l’usinage est adapté à différents types de matériaux, notamment les métaux ferreux et non ferreux, les plastiques techniques ou les composites.
Zoom sur les machines d’usinage
Le processus d’usinage implique l’utilisation d’une machine-outil, telle qu’un tour, une fraiseuse, une rectifieuse ou une perceuse, qui est contrôlée avec précision pour enlever la matière de manière progressive et méthodique. Différents outils de coupe, tels que des forets, des fraises, des alésoirs et des lames, sont utilisés en fonction des besoins spécifiques de l’opération d’usinage.
Au fil des années, l’usinage a évolué avec l’introduction de nouvelles technologies et techniques. Les machines-outils modernes sont devenues de plus en plus automatisées, intégrant des systèmes de commande numérique et des capteurs avancés pour améliorer la précision, la productivité et la sécurité des opérations d’usinage. De nos jours, la plupart des entreprises utilisent ainsi des machines-outils à commande numérique (MOCN), adossée à un système informatique (FAO), ce qui permet d’automatiser partiellement ou totalement la procédure d’usinage.
C’est quoi un technicien d’usinage ?
Un technicien d’usinage est un professionnel qualifié spécialisé dans l’exécution des opérations d’usinage. Il est responsable de la préparation et de la mise en place des machines-outils, du choix des outils de coupe appropriés, du réglage des paramètres de coupe et de l’exécution des opérations d’usinage. Pour y parvenir, il doit être capable de lire et d’interpréter des plans techniques, de sélectionner les bonnes méthodes d’usinage en fonction des spécifications, et d’utiliser avec précision les machines et les instruments de mesure pour garantir la conformité aux tolérances requises.
En plus de ses compétences techniques, le technicien d’usinage doit posséder une solide compréhension des matériaux, des procédés d’usinage et des normes de sécurité. Il doit être capable d’analyser les problèmes potentiels, de résoudre les défauts de fabrication et de prendre des mesures correctives pour assurer la qualité des pièces usinées. Avec l’évolution rapide de l’industrie de l’usinage, les techniciens d’usinage sont par ailleurs tenus de se tenir à jour avec les nouvelles technologies et les avancées du domaine. Ils peuvent en effet être amenés à travailler sur des machines-outils avancées, à intégrer des systèmes de commande numérique et à utiliser des logiciels de conception assistée par ordinateur (CAO) pour optimiser les processus d’usinage.
Quelles sont les 4 opérations basiques d’usinage ?
Le tournage
Réalisée sur un tour, cette technique permet de fabriquer des pièces cylindriques, coniques, ou avec des formes complexes telles que des filetages ou des rainures. La pièce à usiner est fixée sur une broche rotative, tandis que l’outil de coupe est déplacé le long de la pièce pour enlever de la matière et lui donner la forme souhaitée.
Le fraisage
Le fraisage consiste à utiliser une fraise rotative pour enlever de la matière et créer des formes complexes telles que des rainures, des surfaces planes, des poches ou des contours. Les fraiseuses peuvent être utilisées pour l’usinage en 2D ou en 3D, en fonction des mouvements de la pièce et de l’outil de coupe.
Notons que le fraisage de surfaces planes consiste à utiliser une fraise spéciale pour obtenir des surfaces planes lisses et précises. Le fraisage de surfaces planes est souvent utilisé pour réaliser des surfaces d’appui ou des surfaces de référence dans les pièces.
Le perçage / alésage / taraudage
Le perçage est une opération permettant de réaliser des trous dans une pièce à l’aide d’un foret. Le foret tourne et pénètre dans la pièce, en enlevant de la matière pour créer un trou de diamètre et de profondeur précis. Le perçage peut être réalisé sur une perceuse classique ou sur une machine-outil plus avancée.
Complémentaire, le taraudage est une opération utilisée pour créer des filetages internes dans un trou préalablement percé. Un outil de taraud est utilisé pour couper des rainures en forme de filet à l’intérieur du trou, permettant ainsi de visser des boulons ou d’autres éléments filetés.
Enfin, l’alésage vise à agrandir et à améliorer la qualité d’un trou préalablement percé dans une pièce. Cette opération est généralement utilisée lorsque l’on cherche à obtenir des tolérances très précises, des finitions de surface de haute qualité ou des dimensions spécifiques.
La rectification
La rectification est une opération d’usinage de haute précision utilisée pour obtenir des surfaces très lisses et des dimensions précises. Cette opération est réalisée à l’aide d’une rectifieuse qui utilise des meules abrasives pour enlever de petites quantités de matière et obtenir des tolérances très strictes.
Ces opérations d’usinage sont à la base de nombreuses autres techniques d’usinage plus avancées. En fonction des spécifications de la pièce à usiner, des tolérances requises et des caractéristiques géométriques souhaitées, il est important de choisir la bonne opération d’usinage.
La gamme de solutions CAO, FAO, PDM et ERP TopSolid
Quel avenir pour l’usinage ?
Plusieurs grandes tendances sont à noter dans l’univers de l’usinage.
L’automatisation accrue
L’usinage est de plus en plus automatisé, avec l’introduction de robots et de systèmes de fabrication intelligents. Les machines-outils modernes sont équipées de capteurs avancés, de commandes numériques et de technologies d’intelligence artificielle pour optimiser les processus de production, améliorer la précision et la vitesse, et réduire les erreurs humaines.
L’impression 3D pour l’usinage
L’impression 3D est de plus en plus utilisée dans l’usinage, en particulier pour la fabrication de pièces complexes. Les technologies d’impression 3D métallique permettent en effet de produire des pièces avec des géométries internes complexes, ce qui réduit la nécessité d’opérations d’usinage supplémentaires. L’intégration de l’impression 3D et de l’usinage traditionnel offre des opportunités de conception et de fabrication plus flexibles.
La fabrication additive hybride
La fabrication additive hybride combine l’impression 3D avec l’usinage traditionnel. Cette approche permet de construire des pièces avec des structures complexes grâce à l’impression 3D, puis d’effectuer des opérations d’usinage pour obtenir des surfaces finies, des tolérances précises ou des fonctionnalités supplémentaires.
L’intégration de l’intelligence artificielle
L’utilisation de l’intelligence artificielle (IA) dans l’usinage est en expansion. L’IA peut être utilisée pour analyser les données en temps réel provenant des machines-outils, optimiser les paramètres de coupe, détecter les défauts de fabrication et améliorer l’efficacité globale du processus d’usinage.
La durabilité et l’éco-responsabilité
L’usinage du futur se concentrera également sur la durabilité et l’éco-responsabilité. Les entreprises chercheront à réduire leur empreinte environnementale en adoptant des pratiques d’usinage plus économes en énergie, en utilisant des matériaux recyclables et en optimisant les processus pour réduire les déchets.
Médical, aéronautique, mécanique générale ou de précision, métiers du moule ou des outils à suivre, horlogerie, lunetterie, pièces mécano-soudées… Quel que soit votre métier, TopSolid’Cam répond à tous vos besoins en usinage ! Nos différents modules proposent en effet un large panel de solutions techniques pour vos besoins d’usinage en fraisage 2D, 3D, 4 ou 5 axes, en positionné ou en continu et également en tournage et en décolletage. Vous souhaitez en savoir plus ? Contactez-nous !