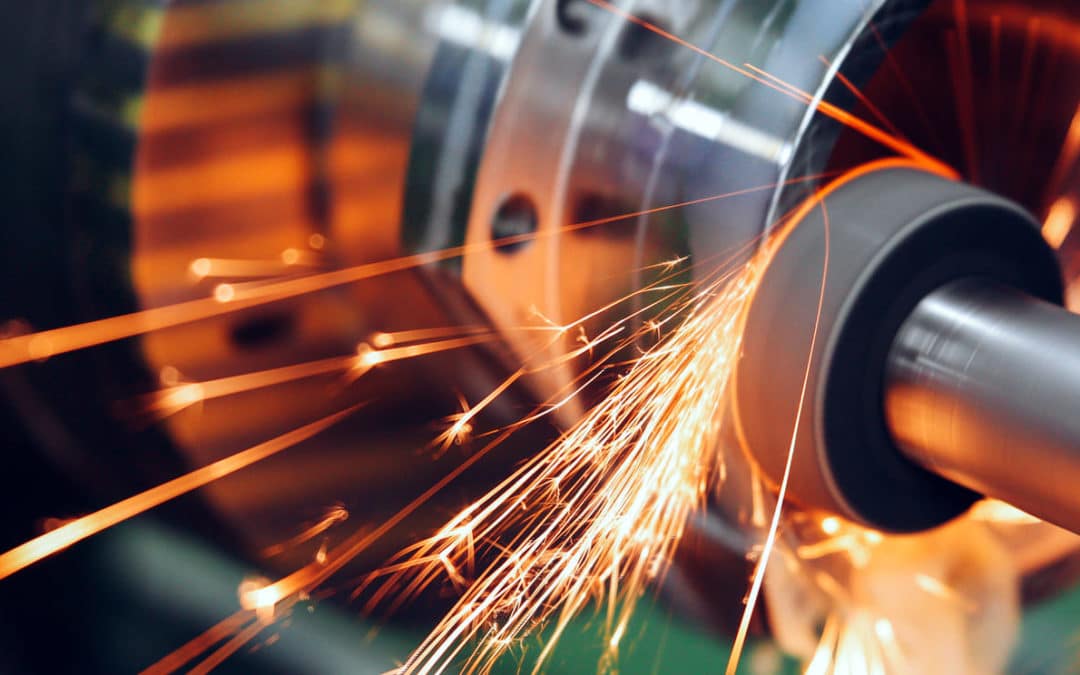
La CFAO au service de la rectification sur vos machines-outils
Les enjeux de la rectification
En utilisant le principe d’usinage par abrasion, la rectification permet d’obtenir une précision dimensionnelle particulièrement élevée sur les pièces, ce qui permet de mieux répondre aux exigences du client. En effet, alors que les opérations d’usinage traditionnelles procèdent par enlèvement de copeaux, la rectification agit plus finement sur la matière en polissant celle-ci à l’aide d’une meule.
Si l’efficacité de cette méthode n’est pas remise en doute, elle constitue néanmoins un investissement important pour les entreprises : celles-ci doivent en effet acheter les machines-outils adaptées à ces opérations. Tout l’enjeu des organisations consiste donc à mesurer la rentabilité des solutions proposées. Pour accomplir des opérations de rectification elles ont alors la possibilité :
- Soit d’investir dans des rectifieuses, des machines dédiées exclusivement à la rectification.
- Soit d’investir dans des machines combinées permettant de faire à la fois de l’usinage et de la rectification.
Les limites d’une programmation « au pied de la machine »
Dans le premier cas de figure évoqué ci-dessus, c’est-à-dire sans solution qui combine usinage et rectification, les entreprises sont contraintes de s’adapter pour créer des programmes de rectification au pied de la machine.
Les inconvénients d’une telle approche sont multiples :
- Manque de flexibilité: contrairement à la FAO, cette programmation ne permet pas de faire la simulation de la machine et les contrôles de collision.
- Coût important: ce type de programmation nécessite d’acheter une rectifieuse en plus de la machine-outil, auxquels s’ajoutent des coûts de manutention.
- Risques d’imprécisions: Le déplacement des pièces de la machine-outil à la rectifieuse amplifie les risques d’imprécision.
- Temps de programmation conséquent : la programmation des machines-outils et le réglage de la rectifieuse peuvent s’avérer chronophages pour les équipes en charge.
Un rapport d’avancement, c’est quoi exactement ?
Vous savez probablement ce qu’est un rapport d’avancement. En revanche, il est fort possible que vous n’en maîtrisiez pas toutes les subtilités ou pire, que vous pensiez que c’est plutôt inutile.
Alors mettons-nous d’accord…
Un rapport d’avancement est un document qui permet de suivre et de communiquer l’état d’un projet, à un moment donné, à différentes parties prenantes. Il fournit une vue d’ensemble des activités réalisées, des tâches accomplies, des résultats obtenus et des problèmes éventuellement rencontrés. Grâce à lui on peut évaluer la progression du projet et prendre des décisions basées sur des informations actualisées.
Un projet de CAO 3D, par exemple pour la conception d’une machine, pourrait inclure les éléments suivants :
- Description du projet : Le rapport peut commencer par une description détaillée du projet incluant l’objectif du projet, les spécifications requises, les contraintes techniques, les exigences fonctionnelles, et les délais prévus.
- Étapes de conception : Vue d’ensemble des différentes étapes de conception suivies pour concevoir la machine en utilisant la CAO 3D. Il peut s’agir de la modélisation 3D initiale, la création des assemblages, l’ajout des fonctionnalités spécifiques, l’optimisation des performances, etc.
- Modèles 3D : Présenter les modèles 3D créés pour la machine à l’aide d’un logiciel de CAO 3D. Ces modèles peuvent montrer la structure de la machine, les composants individuels, les connexions, les mécanismes, etc. Ils servent à visualiser et à valider la conception.
- Résultats des simulations : Si des simulations ont été effectuées pour évaluer les performances de la machine, les résultats de ces simulations peuvent être inclus dans le rapport d’avancement. Cela peut comprendre des analyses de résistance des matériaux, des simulations de mouvement, des tests de collision, etc.
- Problèmes rencontrés : Mentionner les problèmes rencontrés tout au long du processus de conception. Ici, on soulèvera les difficultés techniques, les limitations du logiciel de CAO, les contraintes de fabrication, les retards, etc. Les mesures prises pour résoudre ces problèmes peuvent également être mentionné
- Progression par rapport au plan initial : Le rapport peut fournir une comparaison entre l’état d’avancement réel du projet et le plan initial établi. Cela permet d’évaluer si le projet est en avance, en retard ou conforme au calendrier prévu. Les écarts éventuels peuvent être expliqués et des ajustements peuvent être suggérés.
- Collaborations et communications : Tracer l’historique des interactions avec les autres membres de l’équipe de conception, les fournisseurs, les partenaires ou les clients. Cela inclut les réunions, les échanges d’informations, les demandes de clarification, etc.
- Étapes suivantes : Enfin, le rapport d’avancement peut conclure en mettant en évidence les prochaines étapes du projet. Cela peut inclure les tâches restantes, les échéances à venir, les livrables prévus, les tests à effectuer, etc.
Il est toujours possible de simplifier le niveau de détail des rapports, pour ne garder que ce qui est réellement utile.
Quelle est l’influence d’un rapport d’avancement sur le déroulement d’un projet ?
Les rapports d’avancement s’intègrent dans le processus global de gestion de projet et leur rôle est essentiel.
Ils sont anticipés lors des phases de planification, complétés pendant les phases d’exécution, ils permettent d’identifier les écarts et prendre des mesures correctives lors des phases de suivi et de contrôle, facilitent la communication entre les parties prenantes et enfin, les informations recueillies aident à réévaluer et ajuster le projet.
Si vous voulez faire de bons rapports d’avancement, vous pouvez assez facilement vous y perdre. Alors comment faire pour rendre ça fluide ?
La gamme de solutions CAO, FAO, PDM et ERP TopSolid
La CFAO comme moyen d’optimiser la rectification sur les machines-outils
Devant ces limites, certains fabricants ont développé des machines combinées, qui grâce à la CFAO, permettent :
- D’usiner une pièce en fraisage et tournage dans un premier temps ;
- De rectifier cette même pièce dans un second temps.
Comme les manipulations s’effectuent sur la même machine, la pièce n’a ainsi pas besoin d’être déplacée. Ce mode de fonctionnement permet donc d’éliminer les erreurs de repositionnement dues au déplacement de la pièce du centre d’usinage à la rectifieuse et offre un précieux gain de temps en termes de manutention.
Point d’attention : la nécessité d’avoir un outil CFAO dédié à la rectification
Pour les entreprises équipées de machines combinant usinage et rectification, le choix d’un logiciel de CFAO adapté est donc crucial. En effet, toutes les solutions de CFAO ne contiennent pas des opérations de rectifications dédiées : certaines d’entre elles proposent ainsi de détourner des opérations d’usinage en opérations de rectification. Procédé peu pertinent, car la méthode pour piloter une meule en rectification diffère beaucoup de celle utilisée en fraisage ou en tournage.
Ce type de solution n’apporte donc aucune plus-value au programmeur, contraint d’ajuster manuellement le code ISO afin d’obtenir le bon état de surface sur sa pièce. C’est pourquoi, il est fortement conseillé aux entreprises d’opter pour un outil CFAO qui a pensé l’opération de rectification de manière spécifique.
TopSolid’Cam : un logiciel conçu pour optimiser la rectification sur les machines-outils
Logiciel de CFAO complet et performant, TopSolid’Cam accompagne et facilite la conception des programmeurs grâce à :
- Une intégration facile et complète de la solution ;
- Une interopérabilité avec tous les logiciels de CAO ;
- Un environnement de travail en gestion libre ;
- Une optimisation de la production grâce à un processus de duplication ;
- Différents niveaux de simulation ;
- Une gestion et un suivi des modifications ;
- Une réponse à des besoins variés en fraisage et usinage.
Plus spécifiquement, la fonctionnalité « rectification sur centre d’usinage » proposée par TopSolid’Cam permet aux clients équipés d’une machine-outil combinant usinage et rectification une gestion optimisée de cette opération. En effet, la solution offre la possibilité de programmer la rectification directement depuis le logiciel, avant même que la pièce ne soit montée sur la machine. Conçue spécifiquement pour faire de la rectification sur machine, cette fonctionnalité s’adapte aux caractéristiques de chaque opération et facilite le travail du programmeur.
Vous souhaitez en savoir plus sur la fonctionnalité « rectification sur centre d’usinage » proposé par TopSolid ? Faites une demande de démonstration auprès de notre équipe.